Introduction
Feeling overwhelmed by the endless barrage of questions from your team and customers? Worried about falling behind on crucial projects and losing valuable customers?
You're not alone. It's a scenario that many business owners and managers face every day, and the stress can be immense. But there's a solution — a well-organized process improvement plan.
This isn't just about managing tasks more efficiently — it's about transforming your entire approach to business operations, freeing up your time, and, ultimately, ensuring the satisfaction and loyalty of your customers.
So, in this article, we’ll share everything about the process improvement plan — from its definition to how to create one and improve processes efficiently.
Let’s dive in.
TL;DR: Process improvement plan
- A process improvement plan (PIP) streamlines workflows and enhances efficiency in business operations.
- The plan involves mapping existing processes, setting goals, utilizing resources, creating an action plan, and documenting the new process.
- By engaging stakeholders, using data-driven approaches, and continuous monitoring, businesses can achieve cost reduction, increased efficiency, improved quality, and enhanced customer satisfaction.
- Scribe offers a powerful software solution to streamline the process of creating and implementing process improvement plans.
- Continuous improvement planning involves effective communication, monitoring key metrics, and fostering a culture of ongoing enhancement for sustained productivity and quality improvements.
What is a process improvement plan?
A process improvement plan (PIP) is a strategic document that outlines the necessary steps and information for making changes to workflows and business processes. It provides background information and data on the current processes in place.
Imagine an IT department within a large corporation that is responsible for managing software updates across all employee computers. They observe that the present approach for releasing upgrades is inefficient and frequently causes disruptions in employee productivity.
To solve this, they develop a plan to streamline the update deployment process. This involves investing in automated deployment tools and creating consistent update schedules.
Through this process improvement plan, the company aims to streamline its production line, reduce delays, and improve overall efficiency.
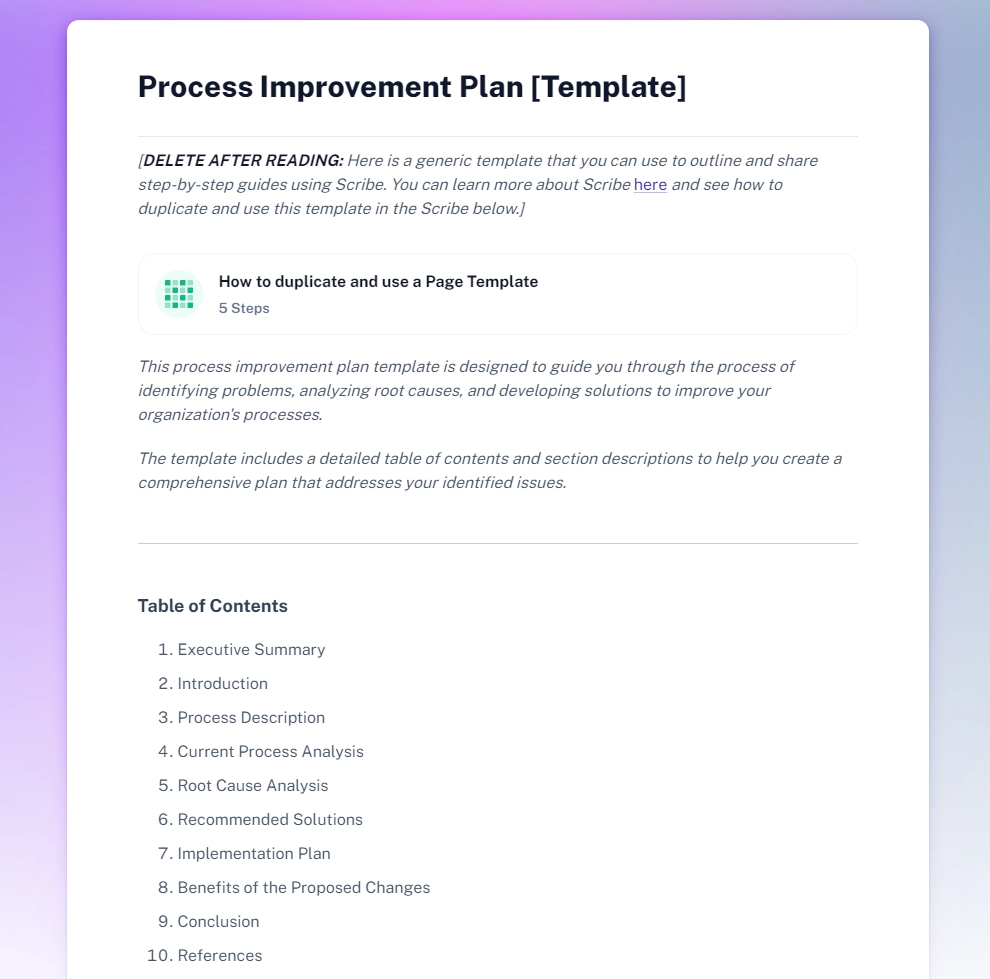
Businesses also use process improvement plan templates to identify problems, analyze root causes, and develop solutions to improve their organization's processes.
Why create a process improvement plan?
There are a ton of benefits to developing process improvement plans, including:
Reduce costs
- Determine areas where resources are misallocated or wasted — allowing for targeted cost-cutting initiatives.
- Eliminate redundant processes and automate tasks to reduce labor costs and improve resource efficiency.
- Direct financial resources toward initiatives that deliver the highest return on investment — optimizing budget allocation.
Increase efficiency
- Simplify complex procedures, eliminate bottlenecks and increase workflow efficiency — allowing tasks to be done faster.
- Ensure resources are utilized effectively and allocated based on job requirements — preventing underutilization or overutilization.
Improve quality
- Identify areas where errors occur frequently and implement corrective actions to prevent defects from arising.
- Encourage ongoing evaluation and refinement to maintain and enhance quality standards over time.
Enhance customer satisfaction
- Align business processes with customer demands and preferences — ensuring that products or services are delivered on schedule and to quality standards.
- Reduce errors, delays, and disturbances in the delivery process, leading to increased reliability and customer satisfaction.
- Identify opportunities to add value to products or services by improving processes, exceeding customer expectations, and fostering loyalty.
Free process improvement plan templates
Use these templates to save time and effort when creating structured plans across projects and departments.
Process improvement plan template
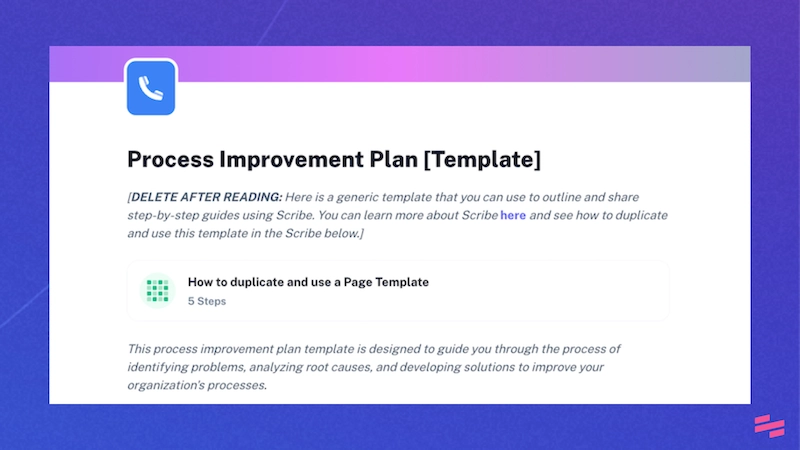
Use this template to create a comprehensive plan to:
- Identify problems.
- Analyze root causes.
- Develop solutions to improve your organization's processes.
👉 Try this process improvement plan template for free.
Plan-Do-Check-Act (PDCA) template
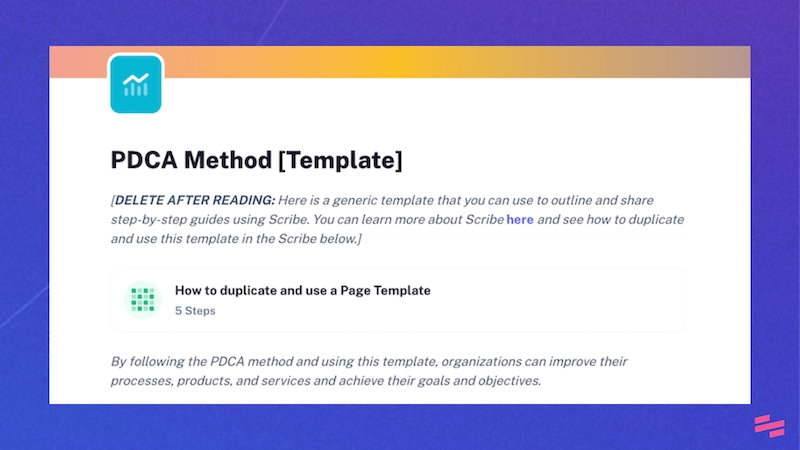
The Plan-Do-Check-Act (PDCA) cycle is a four-step cycle that can be used for any type of improvement project. Use this template to:
- Plan the change.
- Do the change.
- Check the results.
- Act on the results.
👉 Try this Plan-Do-Check-Act template for free.
Continuous improvement (Kaizen) template
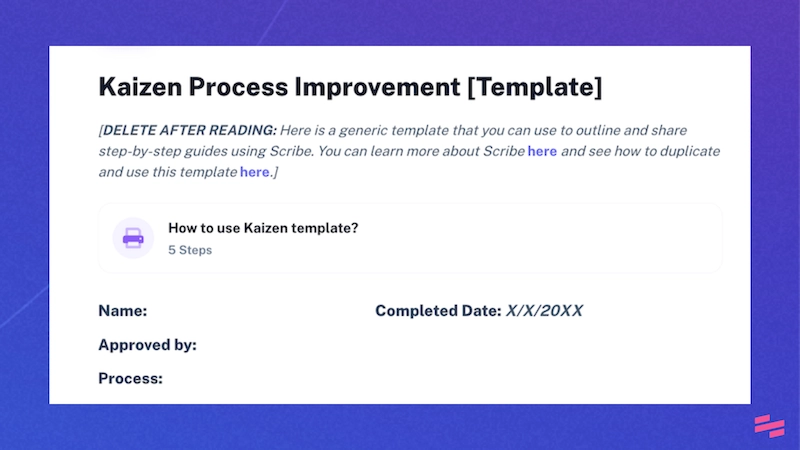
The Kaizen method is a continuous improvement process that helps organizations achieve goals through small, incremental changes.
👉 Try this Kaizen continuous improvement plan template for free.
5S process improvement template
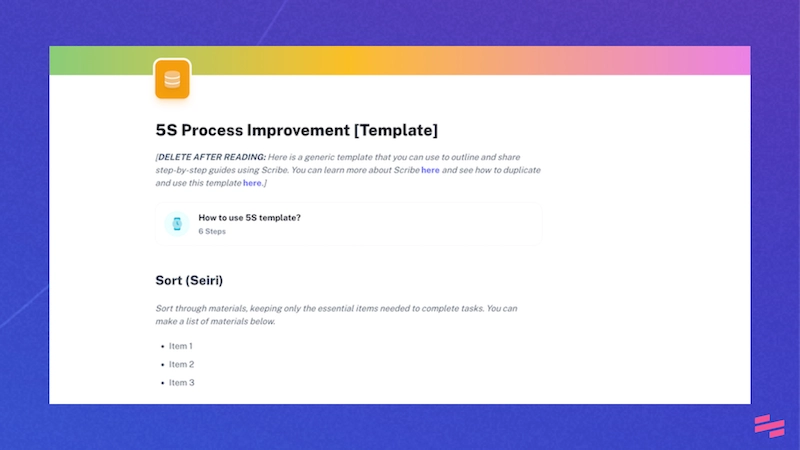
5S is a Lean methodology used to improve the efficiency and organization of a workplace.
Use this template to follow the 5S methodology:
- Seiri (sort).
- Seiton (set in order).
- Seiso (shine).
- Seiketsu (standardize).
- Shitsuke (sustain).
👉 Try this 5S process improvement template for free.
SIPOC analysis template
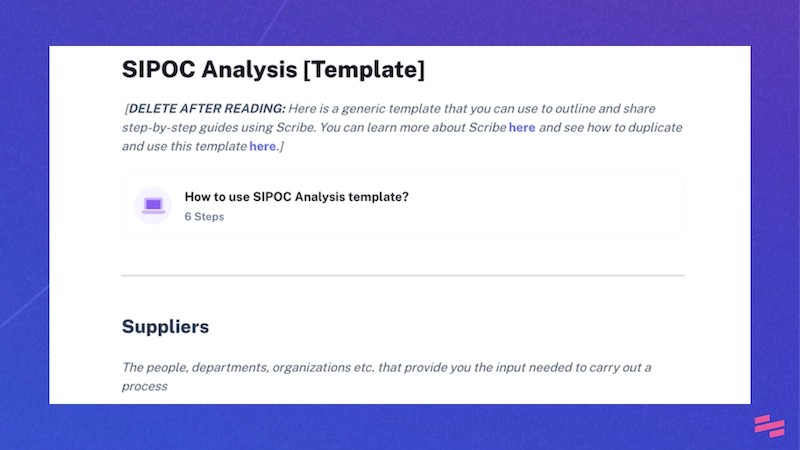
A SIPOC analysis is used in process improvement methodologies such as Six Sigma and Lean to quickly understand the components of a process and identify areas for improvement.
Use this template to create a high-level process map to visualize your:
- Suppliers.
- Inputs.
- Process.
- Outputs.
- Customers.
👉 Try this SIPOC analysis template for free.
100+ free process documentation templates
Try from 100+ free process templates in the Scribe template gallery.

Use these templates to:
- Capture processes and auto-generate documentation in seconds.
- Create training materials for onboarding new employees or introducing changes to existing staff.
- Streamline projects and processes.
... all for half the time in effort.
Best practices for process improvement
Let's start with some helpful best practices that will set you up for success before we dive into crafting your improvement plan.
Always map your existing workflow
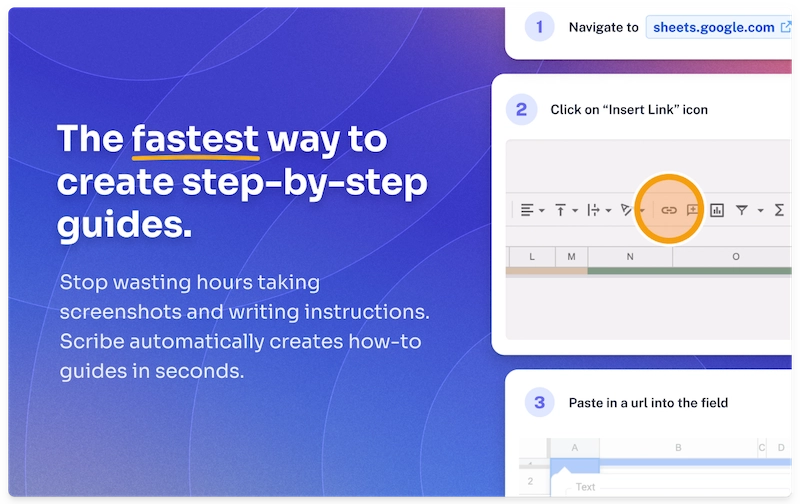
Before you can improve a process, you need to understand it thoroughly. Make a detailed map of your present workflow, including each phase from start to finish.
Process mapping will help you spot inefficiencies, redundancies, and areas for improvement. Define the process to provide a clear baseline for assessing the effectiveness of any changes you make.
Scribe is a powerful software solution designed to streamline the process of creating and implementing process improvement plans. Use Scribe's AI-powered process documentation tool to create a detailed, visual step-by-step guide of the process, like this one:
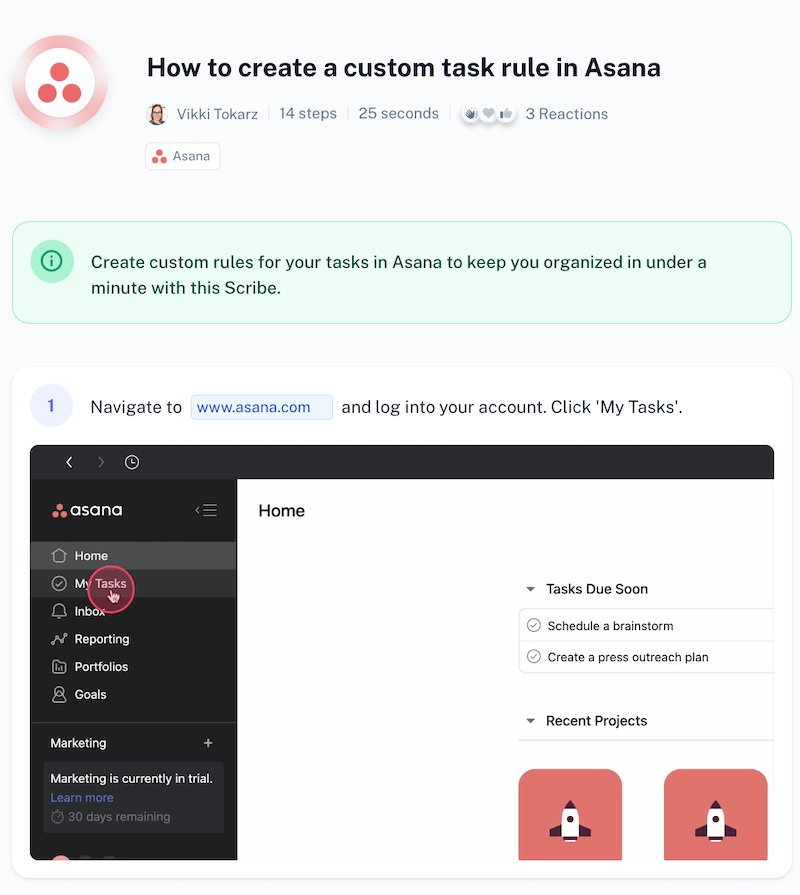
Scribe automatically captures workflows — generating step-by-step guides with screenshots and text in seconds, saving time and ensuring accuracy.
Analyze it and discuss these things:
- Pain points in your process.
- The root cause of any problems.
- Areas of waste or inefficiency.
- Excessive steps, delays, or redundancies.
Define your business goals
Align your process improvement efforts with your overarching business objectives. Clearly define what you aim to achieve through the improvement initiative. Whether your goals are to increase productivity, reduce expenses, improve customer satisfaction, or achieve regulatory compliance, they should be SMART:
- Specific.
- Measurable.
- Achievable.
- Relevant.
- Time-bound.
By focusing on your business goals, you can ensure that process improvements contribute directly to your organization's success.
Precision matters
Be precise and specific when identifying areas for improvement within your processes. Avoid vague or generalized statements, and instead, pinpoint the exact issues that need addressing.
This precision enables you to target root causes effectively and implement solutions that deliver tangible results.
Use a data-driven approach
Base your process improvement decisions on data rather than assumptions or intuition. Gather relevant metrics, performance indicators, and other quantitative data to assess the current state of your processes accurately.
Analyze this data to identify patterns, trends, and areas of underperformance. By leveraging data-driven insights, you can make informed decisions about where and how to implement improvements.
Consider engaging all stakeholders
Engage all key stakeholders in the process improvement plan. This includes:
- Frontline employees.
- Managers.
- Executives.
- Customers.
- Suppliers.
- Any other parties affected by the changes.
Each stakeholder contributes unique viewpoints, expertise, and insights that can benefit the improvement process. Encourage open communication, collaboration, and participation from all stakeholders, and ensure that their concerns, ideas, and criticism are considered.
Want to know about the steps involved in process improvement? Head over to our blog on the process improvement steps for better workflows.
The 7 steps of creating an improvement process plan
Implementing a process improvement plan can be complex, so it's important to understand all the steps involved before starting.
The structure of the improvement plan will depend on the specific needs of your organization. Let's go through the steps for process improvement planning.
Step 1: Map the process you want to improve and analyze it
The first step is to start with process mapping. Visually represent the existing process using flowcharts or diagrams to define the process.
Then examine each step to pinpoint bottlenecks, redundancies, and areas for improvement. Determine if you need to:
- Come up with a good redesign.
- Adjust the process.
- Optimize the process.
- Go back to the drawing board and create a new process.
Look for points where delays occur, resources are underutilized, or tasks are repeated unnecessarily.
Step 2: Identify key areas for improvement
When creating a plan for improvement, these steps can help you brainstorm solutions:
- Where do bottlenecks occur? Identify steps in the process where work slows down or gets stuck due to constraints such as limited resources, outdated technology, or inefficient processes.
- Where are redundancies present? Look for tasks or activities that are duplicated or unnecessary within the process. Adjust the process by eliminating redundant steps and optimizing resource allocation.
- Where are opportunities for optimization? Assess areas where resources are underutilized or where tasks could be performed more efficiently. Consider automation, technology upgrades, or restructuring workflows to improve productivity and reduce waste.
- Ask for feedback: Consult with stakeholders and team members who are directly involved in the process to gather insights and identify pain points. Their input can provide valuable perspectives on areas that require improvement.
Step 3: Decide on your major goals
Define the major goals you want to achieve with the process improvement plan. These goals should be:
- Consistent with your organization's overall strategic objectives.
- Address identified areas for improvement.
- SMART.
Engage the stakeholders who are associated with the process you’re going to improve. Their involvement fosters buy-in and ownership and promotes collaboration across your organization.
Step 4: Define the resources you can use
Identify the resources you’d need to support your process improvement initiatives, including:
- Workers.
- Technology.
- Tools.
- Budget.
And any other assets necessary for implementing the proposed changes.
Step 5: Create your action plan
Develop a detailed action plan outlining the specific steps and timelines for implementing the process improvements:
- Assign tasks to team members.
- Define milestones.
- Set deadlines for each phase of the plan.
- Break down the strategy into manageable tasks, prioritizing high-impact initiatives that align with your goals.
- Consider potential risks and mitigation strategies to minimize disruptions during implementation.
Step 6: Implement the plan
Now you're ready to execute your action plan!
- Communicate the proposed changes to all stakeholders involved, including employees, managers, and external partners.
- Provide training and support to ensure that team members understand their roles and responsibilities in implementing the new processes.
- Monitor progress and keep track of key performance indicators (KPIs).
- Handle any difficulties or challenges that develop during implementation.
- Regularly communicate and collaborate as they are essential for driving successful change within the organization.
Step 7: Document the new process
Make sure you document the new process so that everyone on your team can understand it and follow it consistently.
- Create detailed process documentation, including standard operating procedures (SOPs), workflow diagrams, and training materials.
- Capture key insights, lessons learned, and best practices discovered during the improvement process.
- Make the documentation available to all key stakeholders, whether via a centralized knowledge base or a digital collaboration platform.
With Scribe, you can automatically document processes as you work to create detailed process guides. Capturing your screen as you work, Scribe auto-generates a visual, step-by-step guide with text, links and annotated screenshots.
You can even ask Scribe's generative AI to write your process documentation and improvement plans.
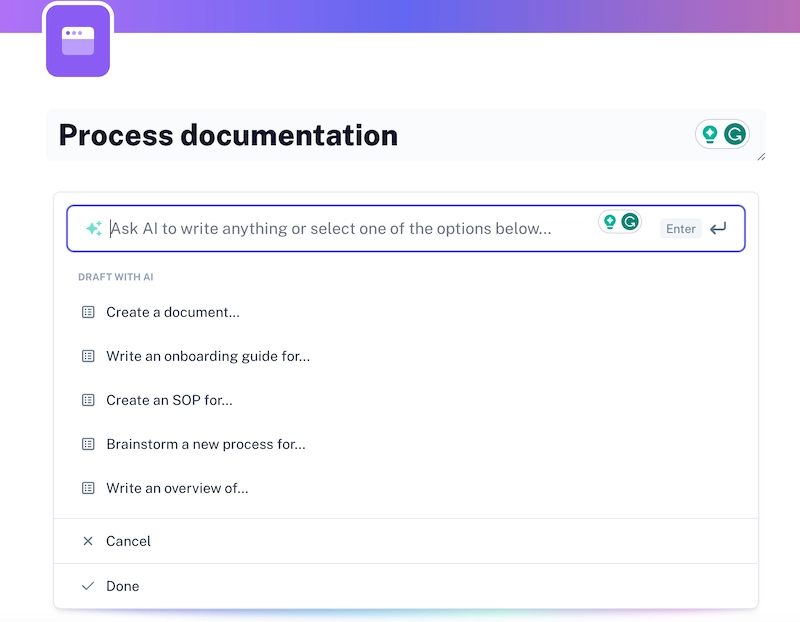
Scribe helps your team adopt (and even love) process improvement plans by:
- Quickly create, share and store your process documentation.
- Make as many process documents as you need, then use Scribe Pages to combine your Scribes with video, images and AI-generated text.
- Creating process improvement templates to standardize your process documentation.
- Compare different versions of processes to track improvement progress and measure the effectiveness of changes over time.
- Facilitate seamless sharing and collaboration on new process designs within the platform — ensuring alignment and engagement among stakeholders.
- Easily share guides with team members with one click, export to PDF or HTML, or embed in your preferred platform.
- Create training materials for onboarding new employees or introducing changes to existing staff using captured process guides.
- Integrate with internal knowledge bases to publish process documentation for easy access and reference.
Don’t simply take our word for it! Sandra Karamitelios, Recruitment Specialist says:
“We have taken all our procedures from an old manual and updated everything — whenever we have a new process or change a process, we use Scribe to document these. Scribe has made this effortless and saved hours and hours and hours of work and time and frustration.”
Be sure to regularly review and update the documentation as you adjust the process over time.
Best practices for continuous improvement planning
1. Communication is key
Maintain open lines of communication throughout the process.
- Include strategies like comprehensive training sessions, open communication channels, and robust change management.
- Tailor your training programs to meet the specific needs of each team member through hands-on training, workshops or online courses.
- Encourage team members to ask questions, provide feedback, and express concerns through regular check-ins and meetings.
2. Measure and monitor key metrics
Continuously measure and monitor your key metrics for maximum results.
- Establish clear goals and objectives for the improvement plan, along with specific metrics for tracking progress.
- Metrics can include efficiency gains, cost savings, customer satisfaction scores, or other relevant KPIs.
- Use tools and software for data collection and analysis to streamline the monitoring process, providing real-time insights into performance trends.
It's always a good idea to conduct regular performance evaluations to keep track of your progress toward your goals. These evaluations can help you identify any deviations and take corrective actions to get you back on track.
3. Optimize for continuous improvement
Viewing process improvement as an ongoing practice can lead to sustained productivity and quality improvements.
- Foster a culture of continuous improvement by encouraging employees to seek enhancement opportunities.
- Implement feedback mechanisms such as suggestion boxes and surveys to gather input from team members.
- Prioritize regular performance monitoring and analysis to identify inefficiencies.
- Emphasize the importance of continuous improvement in driving innovation and maintaining competitiveness.
FAQs
What are the five stages of process improvement?
- Identify the process to be improved.
- Analyze the current process.
- Design the improved process.
- Implement the improved process.
- Continuously monitor and improve the process.
What are the 4 elements of process improvement?
- Identify the need for change: This is the initial step in the Business Process Improvement (BPI) process, where the necessity for change is recognized.
- Analyze the current process: This involves evaluating the existing process to understand its strengths and weaknesses.
- Obtain commitment and support: Securing buy-in and support from stakeholders is crucial for the success of the improvement plan.
- Create an improvement strategy: Develop a clear and actionable plan to implement changes and enhance the process.
What are the 4 most common types of process improvement plans?
The most common types of process improvement plans include Six Sigma, Lean, Total Quality Management (TQM), and Plan-Do-Check-Act (PDCA).
These process improvement methodologies are widely used in various industries to enhance efficiency, reduce waste and improve overall performance.
- Six Sigma aims for near-perfect quality by minimizing defects and variations.
- Lean focuses on eliminating waste and maximizing efficiency.
- Total Quality Management emphasizes continuous improvement and customer satisfaction.
- PDCA is a cyclical improvement method involving planning, executing, checking, and acting.
These process improvement plans often use the DMAIC cycle: Define, Measure, Analyze, Improve, and Control.
Unlock the power of efficient workflows
Ready to transform your business operations and unlock the power of efficient workflows? Don't just map your processes, capture them with Scribe!
Join the thousands of businesses streamlining their success — sign up for Scribe today — it’s free!