Introduction
Many professionals use the terms standard operating procedures (SOPs) and work instructions interchangeably, but they have distinct uses. SOPs outline resources and broad processes, while work instructions include minute details on how to complete a task.
In this guide, we define the differences between SOPs vs. work instructions and provide examples so you can choose which resource is ideal for you.
What Are Standard Operating Procedures?
Standard operating procedures outline organizational processes and routine responsibilities. These formal documents include more than just steps to perform a task — they also feature the process’s scope, purpose, resources and stakeholders. SOPs are shared company-wide and aim to align tasks with business policies and industry regulations.
SOPs organize company processes in an approachable way, gathering all task-relevant resources in one spot. For instance, these documents can contain how-to videos and links to content management system pages.
Here’s how people benefit from an SOP:
- Employees have all the necessary resources to complete a process.
- Managers use SOPs as training materials and to monitor compliance.
- Executives update SOPs to make company-wide changes all at once.
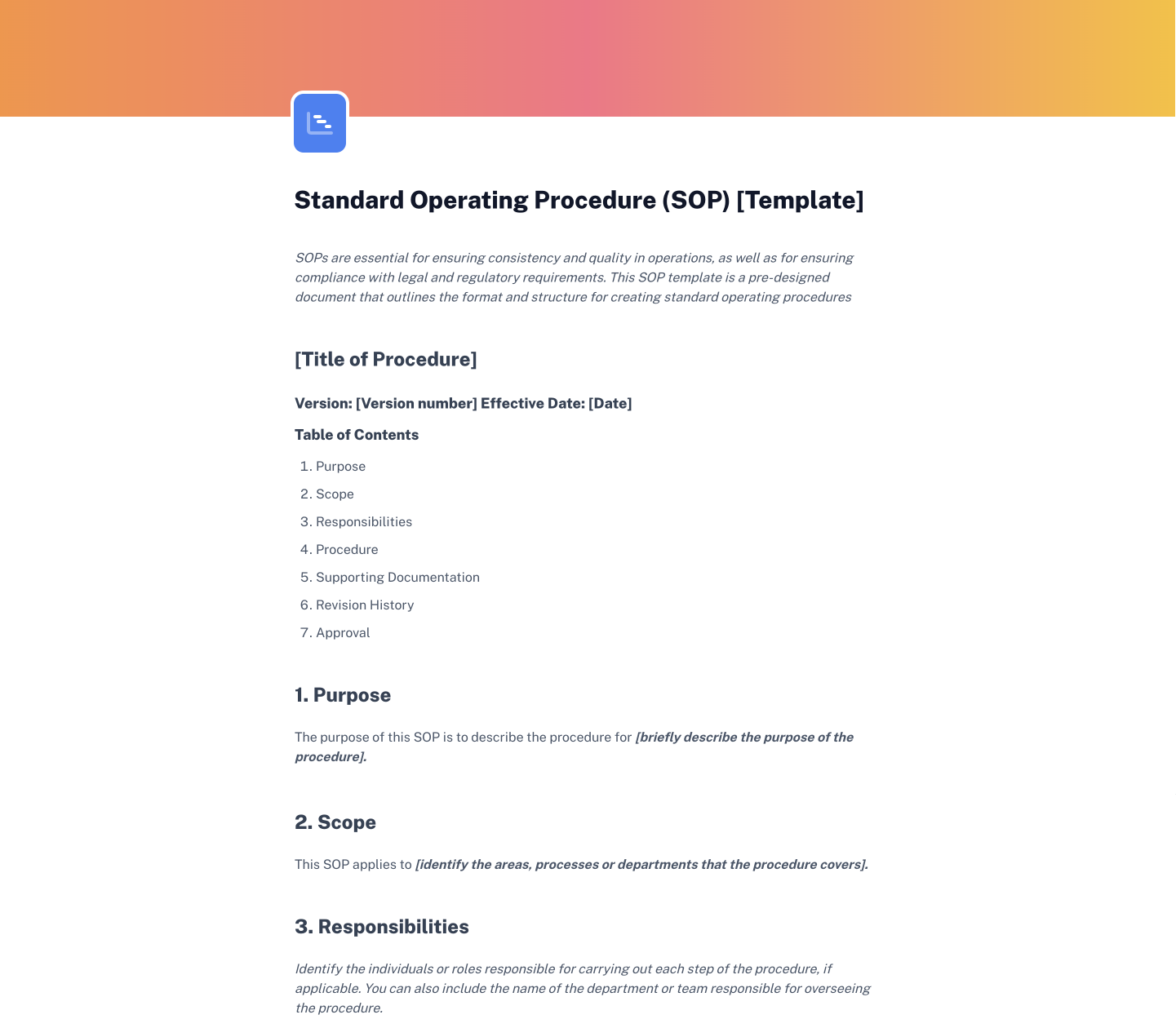
Examples of Standard Operating Procedures
Below are two practical examples of SOPs in different industries that illustrate the main differences between work instructions vs. procedures.
Customer service SOP for resolving customer concerns:
- Purpose: Provide consistent customer service across various locations.
- Scope: This SOP outlines how the customer service department at every location will handle and resolve complaints.
- Responsibilities: Customer Service Representative, Supervisor
- Procedure:some text
- Greet the customer.
- Listen actively to understand the issue.
- Document the problem in the customer relationship management (CRM) software.
- Check for common solutions.
- Provide a solution.
- Confirm understanding with the customer.
- Execute the solution.
- Thank the customer.
- Document the resolution in the CRM.
- Mark the issue as resolved.
- Supporting documentation:some text
- Link to CRM.
- Contact information for the supervisor.
Human resources SOP for pre-onboarding a new employee:
- Purpose: Offer a consistent and in-depth onboarding experience for new employees.
- Scope: This SOP covers all tasks and activities required to prepare for a new hire’s first day.
- Responsibilities: HR Representatives
- Procedure:some text
- Confirm the candidate accepted the offer and completed the necessary paperwork.
- Prepare and send the welcome packet.
- Coordinate with IT to set up the required resources.
- Arrange for workspace setup.
- Schedule orientation, team introductions and initial training sessions.
- Supporting documentation:some text
- Welcome packet.
- Company policies.
- Employee handbook.
- Benefits packet.
- List of employee resources.
What Are Work Instructions?
These resources describe specific tasks in detail, making them essential for compliance, safety and quality assurance. You can’t skip any details when writing work instructions, no matter how small, because these documents aim to minimize employee errors.
Industries where missing minute details could have a significant negative impact, such as manufacturing and healthcare, must use these manuals. But any task that requires consistent outcomes is a good candidate for work instructions.
Here are a few common types:
- Lean work instructions are simple and concise guidelines businesses use for sorting goods, inventory management and product assembly.
- Safety work instructions explain how to keep employees safe in high-risk industries. Examples include personal protective equipment manuals and fire safety protocols.
- Quality work instructions align duties with strict quality standards, often used for quality assurance and manufacturing material inspection.
- Visual work instructions use diagrams and graphs to bridge language gaps. Companies commonly use them for things like safety signs in manufacturing and hand washing procedures in healthcare.
- Project work instructions help team members understand their individual roles within a team, often used in construction and digital marketing projects.
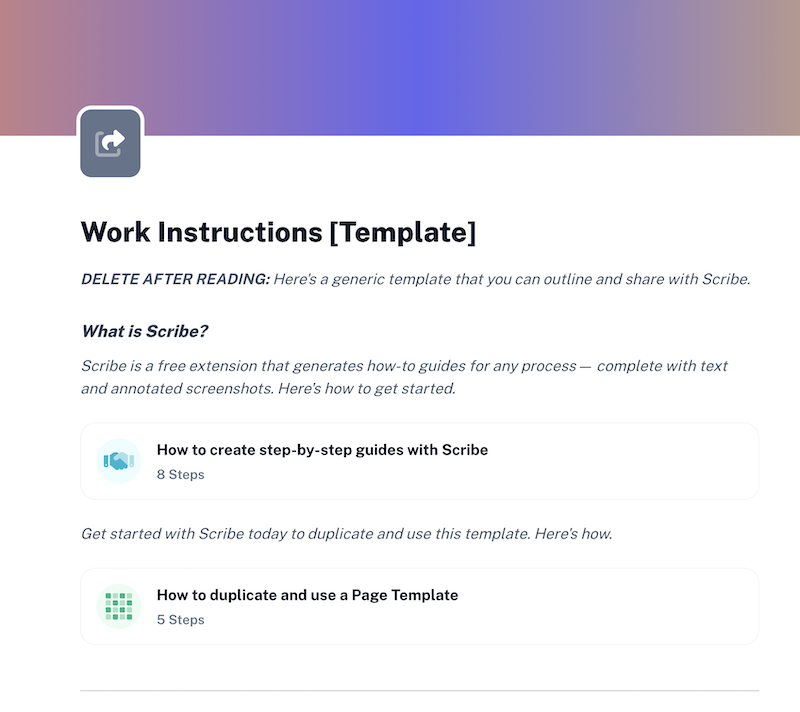
Examples of Work Instructions
Here’s a sample work instruction that further illustrates the differences between working instructions vs. SOPs.
Instructions for cleaning dental tools:
- Gather the following cleaning supplies: some text
- Disinfectant.
- Cleaning brush.
- Soap.
- Put on personal protective equipment:some text
- Gloves.
- Mask.
- Face shield.
- Gown, hat and booties.
- Put the tools in a designated cleaning sink.
- Rinse tools with water to remove loose debris. If available, use an ultrasonic cleaner.
- Apply the disinfectant and use a brush to scrub all surfaces for at least 20 seconds.
- Rinse thoroughly.
- Repeat the process with soap.
- Inspect tools and repeat cleaning if necessary.
While you can work from this example to create SOPs or work instructions, Scribe’s AI tool captures your processes automatically. For even more detail, use Scribe Pages to make one comprehensive set of work instructions with separate Scribes for each process step.
SOPs vs. Work Instructions: What’s the Difference?
SOPs and work instructions are job aids that improve company consistency and efficiency. Both also benefit from best practices like process mapping and using premade templates. The key difference between standard operating procedures and work instructions is the level of detail.
SOPs outline the processes and desired results to reach company standards. Most SOPs assume employees know small details and only need information on overarching steps.
For example, an SOP for preparing a recipe at a restaurant could include a step about washing your hands that reads, “Wash your hands.” But the SOP doesn’t include turning on the sink, grabbing soap and washing between your fingers.
On the other hand, work instructions are step-by-step guides that include every step. They’re essential references for ensuring consistency and compliance by doing the exact same thing each time.
Note that this level of detail isn’t because employees don’t know their roles. Instead, work instructions must contain specific steps to align with quality and safety guidelines. In this document, the hand washing step could instruct: “Wet your hands with clean water, apply soap and scrub all surfaces of your hands for at least 20 seconds.”
When To Use SOPs
Writing an SOP is ideal when you want to enhance org-wide consistency. They’re best when you have a group of professionals who possess industry knowledge and need to know how to complete tasks to company standards.
We recommend SOPs for many processes, including:
- Customer service calls.
- Marketing content reviews.
- IT troubleshooting.
- Sales objection handling.
- Employee exits.
Browsing SOP templates is the best way to determine whether they suit your processes. Our ultimate guide on how to write SOPs has over 100 templates you can download and customize.
When To Use Work Instructions
Work instructions lay out obvious details you wouldn’t normally think to say, which is best for educating employees new to a process or who must follow detailed steps to align with regulations.
We recommend work instructions for tasks that are high-risk or require consistency, such as:
- Auditing financial statements.
- Administering medication to patients.
- Inspecting delicate software.
- Making signature drinks at a restaurant.
- Submitting documents for client review.
To make these documents quickly, start with a customizable template to organize your thoughts.
Build Logical Guides With Scribe
People perform tasks more efficiently when they understand the steps and protocols involved. Both SOPs and work instructions help eliminate uncertainty by providing precise directions for completing tasks. To decide which type to create, consider how in-depth your documents need to be.
No matter which you choose, Scribe streamlines the task documentation process. The AI tool captures your on-screen activities and generates detailed guides complete with screenshots. And you can easily insert GIFs, format text and add in-doc tips to customize the outline to suit your needs.
Sign up for Scribe today and enhance organizational consistency and productivity.