Introduction
Basketball team players often play against each other to utilize the strengths of each player and repeatedly hone their strategy as defined by the coach.
Repeating this process over and over throughout the course of the season helps players develop a chemistry that gives the team an edge over its competition, ultimately leading to success.
The same is true in the business world to continuously improve and succeed.
If your team works together to achieve the same goal and diligently follows the repeatable process improvement steps, it’ll develop a new chemistry between co-workers and nurture continuous improvement.
But not all process improvement tactics are guaranteed to work.
You have to track what’s working and what isn’t to ensure better outcomes.
In basketball, you can count the number of baskets scored and the games won. In the business world, you need process improvement metrics that can help you assess and improve operational performance across your company.
Which process improvement metrics make more sense for your business? Let’s find out.
What is process improvement?
Process improvement, also known as business process improvement, involves removing inefficiencies and redundancies in existing processes and workflows that often lead to project delays, productivity decline and employee demoralization.
Instead of being a one-time activity, process improvement is an ongoing exercise to make processes faster, more efficient and more accurate.
Why is process improvement important?
Process improvement allows you to accomplish business goals and meet market demands with minimal wastage.
Processes define how things should be done to achieve consistent results, making them fundamental to an organization’s culture. With organizations constantly changing to keep up with internal and external pressures, continuous process improvement becomes necessary to reflect these changes and ensure continued growth.
Here’s what a typical process improvement cycle involves:
- Addresses your organization’s existing processes, their relative health and their roles concerning your end goals.
- Identifies broken processes and optimizes them to better align with your organizational goals.
- Defines how to improve processes so they add more value to the core operation.
- Organizes available resources, including manpower, IT and other systems, for effective process improvement implementation.
Essentially, process improvement will make your business the best it can be, facilitating growth and innovation.
15 Metrics for process improvement & KPIs you need to know
Process improvement metrics and key performance indicators (KPIs) are the measurement standards and benchmarks you can use to analyze and assess the performance, progress and quality of a business process.
With the right metrics, you can capture process data to identify one of the following two problems:
- Process that was modeled incorrectly. For example, inadequate manpower or missed deadlines.
- Person responsible for the process was inefficient. For example, certain tasks weren’t updated or tasks weren’t assigned on time.
At this point, you’re probably wondering what are the right metrics to track your process improvement efforts. Here you go:
1. Productivity
Productivity measures how much of a process you can complete within a stipulated time period, usually in hours. It’s typically represented as a ratio, showing how much you‘ve produced and the resources you’ve used to achieve it.
The productivity metric is useful for comparing the performance of two employees, techniques and processes. For example, if Worker A makes three bags in one hour and Worker B makes two bags in one hour, their productivity ratio will be 3:1 and 2:1, respectively.
This makes Worker A more productive as they can make more products in less time.
2. Efficiency
The efficiency metric indicates the ratio of input and output and highlights how much waste exists in your production cycle. In other words, how quickly you can get a task completed accurately—or the best way to create something with the least amount of resources.
Suppose you want to figure out how efficient your production process is. You’ll have to consider the total amount of time taken to make the products in relation to the entire length of the process, from buying raw materials to delivering the product.
3. Timelines
Timeliness measures if your team is able to complete a specific process within a predefined time frame.
For example, if you promise a customer delivery within five days, timeliness determines whether your newly improved process is productive and efficient enough to ensure you meet that deadline.
4. Return on investment (ROI)
The ROI metric tells you whether your organization is generating enough profit to justify the total investment in implementing process improvement methodologies. It’s expressed as a percentage.
For example, if you’ve spent $100,000 automating manual processes and managed to rake in $500,000 worth of investments, your ROI will be [(500,000-100,000) / 100,000 x 100] 400 percent.
5. Rate of production
The rate of production or throughput indicates the total output in a given time period. Unlike productivity, the rate of production doesn’t take into account the quantity of items produced but how fast your team can produce them.
For instance, if your team is tasked with producing 200 units of bags in 100 hours, their rate of production will be 2 bags an hour.
6. Takt time
Takt time refers to the total amount of time taken to finish producing one unit before making the next.
Suppose your team takes one hour to bake a batch of cupcakes. This means their takt time is one hour and they can start working on a new batch every hour.
7. Cycle time
Cycle time refers to the total time taken to complete the process from beginning to end.
Depending on the process, the cycle time of a process can be in hours, days or years. For example, the average time for resolving a customer query can be a few hours, while the process of producing and delivering products will likely be expressed in days.
8. Error rate
Error or failure rate calculates the number of errors made throughout the production process. It’s typically represented as a percentage and factors in the total number of units produced against the total number of units that failed quality control.
For example, if your production team produces 10,000 T-shirts, out of which 500 have some defect in the form of wrong sizing or bad stitching, your error rate will be 20 percent
9. Quality rate
Your organization’s quality rate is the opposite of your error rate. It tells the total number of products or units produced that meet your quality standards.
10. Effectiveness
Process effectiveness measures your expected results against your actual results. Ideally, you want the effective rate to be hundred percent, where your actual results meet your expectations in terms of time, cost and quality.
11. Cost-effectiveness
This process improvement metric measures how much it costs to achieve a benefit. Use it to calculate monetary factors (cost per unit) and measure non-monetary factors (health outcomes).
12. Competitiveness
The competitiveness metric presents your relationship with your market rivals as a percentage. It factors in your organization’s current market share to understand how much control you have over your target audience.
For example, if your company’s total sales revenue is $200,000 annually and the total sales revenue of the entire industry is $2 million, your company’s total market share will be 10 percent.
13. Turnaround time
Turnaround time measures how long it takes your team to get the product in the customer’s hands.
Since this metric is considered from the customer’s perspective, you’ll factor in the time from placement to delivery.
Suppose a customer places an order on your website and you tell them the turnaround time is five days. This means, from the time they placed the order, it’ll take five days to find, fill, ship and deliver their order.
14. Capacity
Capacity measures the maximum number of units or items you can produce in a given time period.
Note that capacity isn't the same as productivity and rate of production. The metric determines the best output your organization can achieve if all factors worked perfectly.
15. Value
The value metric determines what a customer thinks your product is worth against the asking price. Any product can have a good or bad value depending on factors like necessity, competition and location.
A common example is charging rent based on location. Customers will find a one-bedroom apartment in a small suburb at $3,500 exorbitant, but will likely be okay paying the same amount for a similar apartment in a metropolitan city.
How to apply process improvement metrics to strengthen business processes
The following are some easy tips to implement metrics and strengthen your existing processes:
Define the appropriate metrics
Identify the right metrics for your organization using the SMART (specific, measurable, achievable, relevant, time-based) methodology.
This will help you identify the most suitable metrics to strengthen your existing processes. Make sure the goals you set are achievable as there’s no point in setting targets that cannot be achieved. Your staff may also feel defeated before they begin, lowering team morale.
Understand how to collect the required data
Companies often set process improvement metrics only to discover that either their processes or tools — or both — cannot provide them with the necessary data. Before spending money, be clear on how much your business will benefit from having the metric.
To ensure real progress, everyone involved should agree to collect the data in exactly the same way across single or multiple departments, offices and branches and nationally or internationally.
Wondering how to standardize metrics? Use Scribe to create step-by-step guides and templates outlining how to calculate finalized process improvement metrics.
What’s more, you can use Scribe Pages to combine multiple guides (Scribes) along with videos, images and more in large process documents. This way, you can cover everything your team needs to know about collecting data and calculating the metrics.
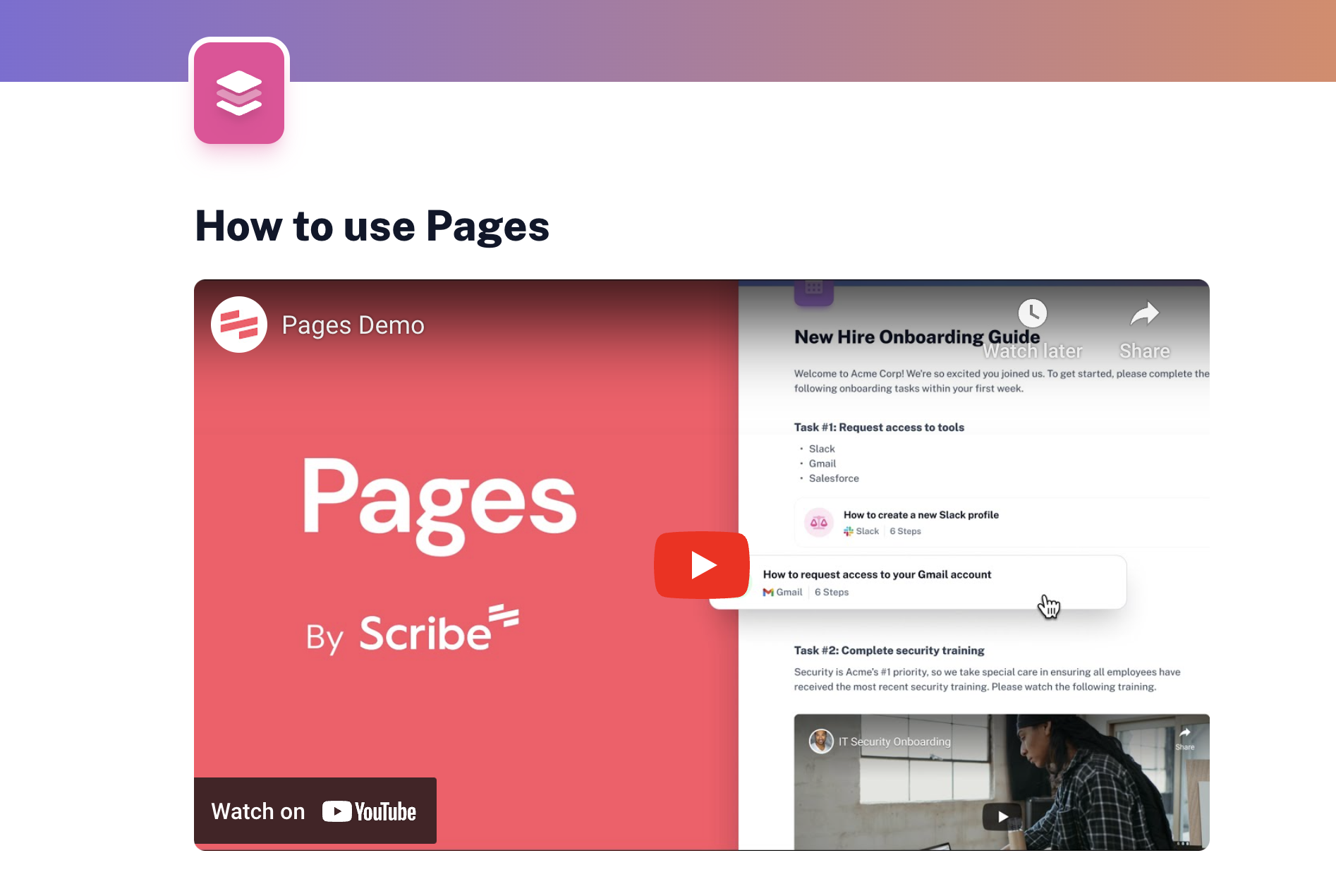
Encouraging continuous process improvement
Another critical aspect of implementing process improvement metrics is to revise time from time to time for relevance.
As time goes by, your organization will evolve and several changes will surface. So changing metrics to ensure what you’re measuring and prioritizing becomes necessary to improve business and set realistic but challenging targets.
Also, keep an eye for the latest process improvement examples to stay on top of trends.
Process improvement metrics in summary
And that’s it—that’s everything you need to know to get started with improvement metrics and strengthen your existing processes. While the process itself may seem complicated, it’ll become significantly simpler once your team gets a hang of how to go about things.
And of course, you can always document steps to standardize processes and metrics with Scribe.
Try our super user-friendly and fast process documentation tool, and make a Scribe yourself.