Introduction
It’s time to revamp your company’s business processes. Where shall you start?
With an abundance of things requiring optimizing, you must be puzzled not knowing how to structure process improvement. Luckily, you aren’t the first to go through it.
We’ve looked into the experience of different companies optimizing their operations to share the best process improvement examples and ideas with you. Read on to find:
- The most effective process improvement frameworks.
- Case studies of companies that have done process improvement successfully.
- Six process improvement ideas to start with.
📌 Related resource: Decoding the Truth: 6 Process Improvement Myths
5 Process improvement frameworks
There are about a dozen of process improvement frameworks. We recommend that you pay attention to the following five methodologies.
1. Six Sigma
Six Sigma is a business improvement framework aimed at minimizing the number of variations within the end product and reducing defects. It’s most commonly applied in manufacturing.
The framework has two main methods: DMAIC (Define, Measure, Analyse, Improve and Control) for existing processes and DMADV (Define, Measure, Analyse, Design and Verify) for new processes.
Each method of Six Sigma uses a statistical methodology to minimize the likelihood of error and improve profits.
2. Kaizen
Kaizen is a continuous improvement model aimed at optimizing processes to get rid of any waste.
It focuses on removing three types of waste: redundant effort, overproduction, and resource exhaustion.
3. Plan-Do-Check-Act (PDCA)
PDCA is an interactive management method that presents process improvement as a cycle. It allows operations managers full control over the improvement process, minimizing risks that change might bring.
It’s a powerful framework for those who want to gradually improve processes without disturbing existing workflows before you’ve proved the effectiveness of new methods.
4. Total Quality Management (TQM)
Total Quality Management (TQM) is a strategy focused on achieving long-term success by improving customer satisfaction. TQM is often used by manufacturers to improve supply chain management.
If your ultimate goal is to benefit the end customer through optimizing business-centric processes, you may want to try TQM as a process improvement strategy.
5. Business Process Management (BPM)
BPM is a methodology that aims at reducing process complexity, automating manual work and removing bottlenecks to achieve higher efficiency. The five steps of the process management lifecycle include:
- Analyze.
- Model.
- Implement.
- Monitor.
- Optimize.
The framework starts with process mapping and evolves into continuous monitoring and improvement.
5 Real-life process improvement examples
Companies in different industries apply process improvement principles to achieve higher efficiency. Here’s how brands in banking, safety, retail, healthcare and manufacturing do it.
1. Howard Bank
Howard Bank, recently acquired by F.N.B. Corp., was looking to optimize the client account opening process to have more time to talk to new customers and discover their financial needs.
To achieve this goal, Howard Bank:
- Developed a paperless account opening process.
- Consolidated all critical business data.
- Automated the process wherever possible.
As a result of process improvement, Howard Bank reduced the time to open an account from 90 to 20 minutes. Not only did it give account managers more time to interact with customers but also improved customer experience and made staff members’ jobs easier.
2. EDEKA
EDEKA, a German supermarket corporation, was looking to improve processes, particularly in the IT department. With a neverending flow of tickets, the team was struggling to structure work and resolve issues promptly.
To accelerate operations, EDEKA had to implement a new analytics solution that provided the IT service desk with a full overview of all systems and let them identify root causes in a few mouse clicks. They also standardized the key ticket assignment and resolution processes and used predictive analysis — to better plan the workforce when incidents were most likely to happen.
After improving service desk processes, the IT department managed to decrease solution times and reduce workload.
3. 3M
In 1975, 3M, a multinational conglomerate committed to environmental stewardship and sustainability, launched the Pollution Prevention Pays program aimed at eliminating pollution through product design. They were among the first enterprises to implement Six Sigma to achieve sustainability goals such as reducing energy use, air emissions, waste, etc.
The initiative involved:
- Training thousands of employees to the Six Sigma methodology.
- Leveraging as much data as possible.
- Moving to the cloud and digitizing operations.
- Increasing production speed.
- Minimizing operational waste.
These are the results 3M achieved between 2000 and 2005:
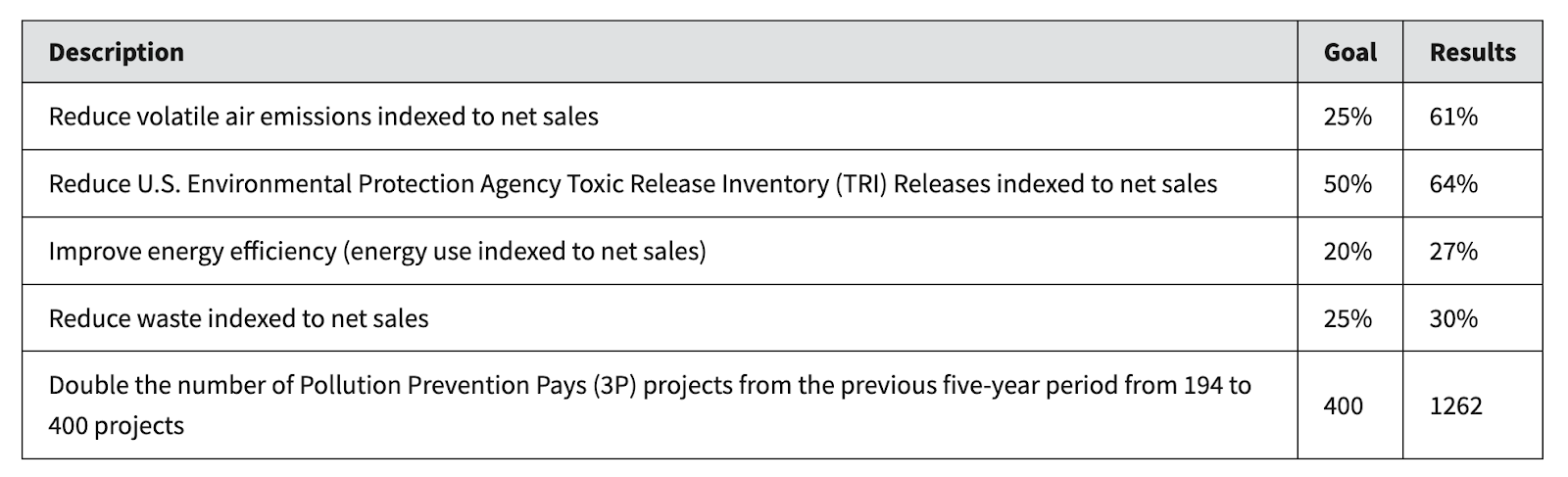
4. CooperVision
CooperVision, one of the biggest manufacturers of soft contact lenses, needed to overcome the challenges of managing several product lines while maintaining decent quality and minimizing defects. Their manufacturing processes weren’t designed well before they turned to process improvement.
The company started by getting the leadership on board with the initiative, pinpointing the problems and choosing the methodology. By following the DMAIC framework, CooperVision achieved a 75 percent improvement in productivity and a 70 percent reduction in quality defects.
5. Lockheed Martin
Lockheed Martin, a global security and aerospace company, has created a continuous improvement culture to stay competitive and never stop embracing change. They:
- Established quality metrics (e.g. defects per million opportunities (DPMO)).
- Introduced information systems for paperless operations.
- Integrated production and quality assurance across operations.
- Documented the key procedures like Root-Cause Analysis and Corrective Action.
- Automated quality control procedures.
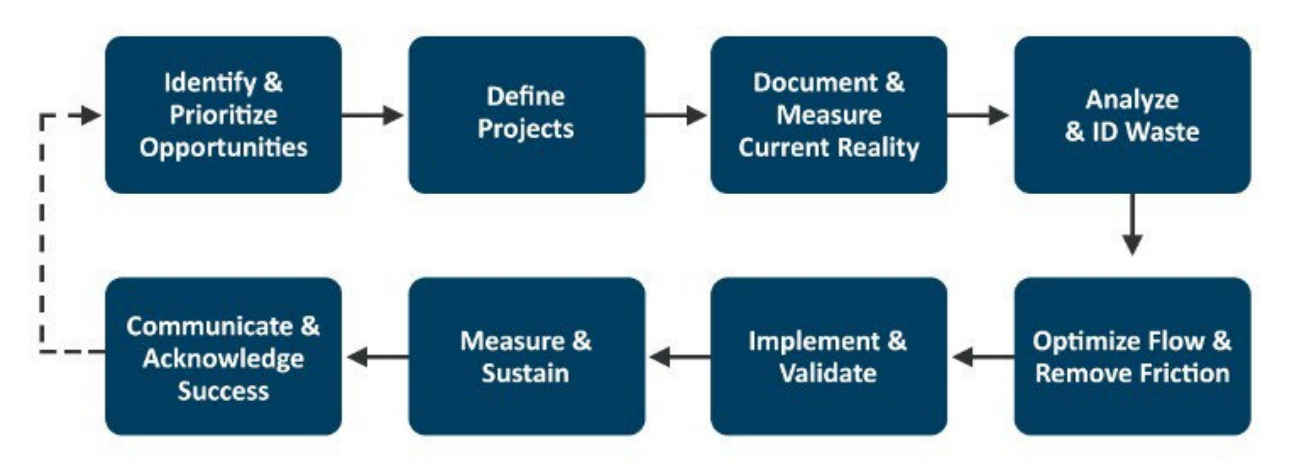
Through continuous process improvement, Lockheed Martin achieved a 46.9 percent reduction in scrap/rework costs.
6 ideas for business process improvement initiatives
Enough of success stories. Now, it’s your turn to improve business processes.
We’ve come up with six process improvement steps you should include in your continuous improvement strategy.
1. Optimizing the hiring process
To make your hiring process more efficient, standardize it. These very simple actions will help you set HR operations up for continuous improvement:
- Implement HR software to centralize all the candidate data.
- Create a job description template.
- Design custom application forms.
- Introduce regular training for HR reps.
- Automate recruiting process follow-ups.
- Document your reinvented HR process.
Implementing HR management software is going to be the biggest step toward improving the recruiting process. You may need to follow the PDCA cycle to help your team embrace this big change and shift to a new system successfully.
Even if you use one already, there are surely a lot of hidden opportunities your HR team has been missing out on. Spend time monitoring how people use your HR technology to identify features you haven’t adopted properly.
💡 Check out our list of the best HR Chrome extensions for recruiters!
2. Creating employee onboarding flows
If you’re hiring actively, new employee onboarding and training must take plenty of productive time from your senior-level employees. How can you improve business processes while your best talents are stuck with unproductive work?
Don’t worry, it’s just a rhetorical question. We're not trying to downplay the importance of onboarding. What you should do is optimize onboarding workflows before you proceed to improve other processes.
Here’s how you can create an effective onboarding program:
- Invest in onboarding software.
- Develop a pre-onboarding checklist.
- Create in-app guidance for business software.
- Automate access granting and other basic tasks.
- Prepare training materials, like video tutorials, step-by-step guides, articles, tests, etc.
- Write an employee handbook if you haven’t done it yet. Try Scribe's free onboarding guide maker to get started!
Similar to any other process, onboarding will benefit from automation. That’s why investing in HR software is on top of the list again. Make employee onboarding automation the key priority of your onboarding process improvement initiative. Soon you’ll see reduced onboarding time, improved onboarding ux (user experience), and increased productivity in every team in the company.
3. Automating help desk processes
IT teams of huge brands like EDEKA aren’t the only ones struggling to handle large volumes of incoming help desk requests. Your IT department also needs process improvement.
You can automate help desk processes by:
- Implementing help desk software (but you already have one in place, right?).
- Setting up automatic capturing and logging of all incoming requests.
- Defining rules for automatic assigning of issues to relevant help desk technicians based on their skills and current capacity.
- Defining rules for automatic prioritization of issues.
- Dynamically capturing successful fixes and turning them into auto-generated guides (haven’t heard how Scribe does it yet?).
- Setting up notifications to inform everyone involved on the status of requests.
- Creating automated workflows to deal with repetitive, basic tasks.
- Building IT policies that help your team create scalable and reusable procedures for responding to change.
While an automated ticket routine is hardly a new approach for your IT team, the idea of automating some of the repeatable tasks might be new to them. For instance, they may write scripts that will facilitate password reset requests without any human intervention. Automation of onboarding journeys will also take some burden off your IT team and improve IT department productivity.
4. Fostering digital transformation
It’s not only ticket assignments or HR processes that can be automated. Every team in your company will benefit from implementing new technology and automating the most time-consuming processes. It’s also known as digital transformation.
Alongside implementing new software, digital transformation fundamentally changes the way the company operates and (hopefully) optimizes internal processes. That’s why it must be a part of your process improvement strategy.
To carry out it successfully — either within a particular team or company-wide — you need to follow these digital transformation examples:
- Use operational surveys, process mapping and cause analysis to identify bottlenecks and weak points in the workflows.
- Create a process improvement plan.
- Highlight the processes that will benefit from automation.
- Find process transformation software that fits your needs and budget.
- See how this software will resolve your problems (you might need help from their customer support).
- Design workflows.
- Develop interactive workflows, in-app guidance and training materials to help employees adopt new software.
- Set up tracking and reporting to measure digital adoption.
- Continue to follow technology trends, optimize workflows and upskill employees to support continuous improvement.
📌 Related resource: 7 Digital Transformation Trends to Know About
5. Centralizing company knowledge
We can’t stress enough how important it is to document your knowledge. Creating strategies for knowledge management prevents knowledge loss but also improves business processes a lot.
As a part of your business improvement initiative, create a knowledge base and fill it with workflow documentation, training materials and other resources that will help your employees to do their job better.
Follow these knowledge sharing best practices and your internal processes will never be the same:
- Create a company wiki.
- If you have one, revisit and update it.
- Use Scribe to auto-generate step-by-step guides to new business processes. Don’t spend a second writing your documentation.
- Answer FAQs and make sure your internal knowledge base is linked in multiple sources (Slack, website, collaboration tools, etc.).
- Encourage employees to continue documenting workflows.
- Assign a person responsible for auditing the wiki regularly.
Check out these step-by-step playbooks on how to create a wiki using popular platforms like OneNote, SharePoint and GitHub:
6. Reducing SaaS costs
Assuming you’ve already gone through digital transformation and have a bunch of tools in your tech stack, there’s something you should do to make the most of this investment. You should optimize your SaaS costs.
Follow this simple 6-step strategy to improve your SaaS management process and reduce technology infrastructure costs:
- Make a list of all your SaaS tools.
- Spot overlapping features and duplicate applications (do your marketing and sales teams use different CRMs?).
- Consolidate your IT infrastructure.
- Create a standard workflow for technology requesting and procurement.
That’s it. You’re ready to take your first steps into process improvement!
Process improvement = process standardization
The biggest problem with inefficient processes is a lack of standards. As you improve your workflows, create standards and document everything. Your team will perform much better once they have consistent processes in place.