Introduction
Quality control determines a business's success as it helps to ensure your team delivers only top-notch products and services. Understanding what cost of quality (COQ) is would help you determine the costs of maintaining high-quality products and services and the potential costs of failures.
Therefore, this article aims to provide insights into COQ (also known as quality costs), share the effects of poor quality assurance and examine prevention costs — including tips on how to use and measure them.
What is Cost of Quality (CoQ)?
Wikipedia defines the cost of quality as a means to quantify the total cost of quality-related efforts and deficiencies. It was first described by Armand V. Feigenbaum in a 1956 Harvard Business Review article. Before its conception, the general notion was that you had to invest in higher costs and resources to produce high-quality products — which could be achieved by buying better materials or machines or hiring more labor.
The American Society for Quality (ASQ) defines CoQ as
"a methodology that allows an organization to determine the extent to which its resources are used for activities that prevent poor quality, that appraise the quality of the organization’s products or services, and that result from internal and external failures."
"Therefore, having such information allows an organization to determine the potential savings to be gained by implementing process improvements," the body adds.
Six Sigma allows you to figure out the cost of quality by estimating the following:
- The cost of production of the wasted original product.
- The cost of the recall.
- Scrapping or rework.
- Additional work done to rectify the original product.
- The resultant cost of the recall.
- The cost of manpower working with the product before, during and after the recall.
- The cost of losing business.
- Bad publicity.
- Their impact on stock price
- The delay in working on another product or another feature for the same product.
Additionally, the cost of quality can be represented by the sum of two factors: the cost of good quality and the cost of poor quality equates to the cost of quality — as shown in the equation below:
CoQ = CoGQ + CoPQ
Summarily, we can deduce that the goal of calculating the cost of quality is to create an understanding of how quality impacts the bottom line. Cost of quality allows manufacturers to analyze and improve their quality operations.
🎓 Related reading: How to Build Powerful Logistic Management Processes That Optimize Your Supply Chain
What is the cost of poor quality?
According to the ASQ, the cost of poor quality (COPQ) refers to the costs of providing poor quality products or services. The cost of poor quality is divided into three categories:
- Appraisal costs incurred to ascertain the degree of conformance to quality requirements.
- Internal failure costs related to defects found before the customer receives the product or service.
- External failure costs associated with defects found after the customer receives the product or service.
Furthermore, quality-related activities that incur costs may be divided into prevention, appraisal, and internal and external failure costs.
How to calculate your cost of quality
Most times, organizations measure their Cost of Quality by calculating total warranty dollars as a percentage of sales. However, this method is flawed because it looks externally at the CoQ and not internally.
So, how do you calculate it?
You need to track the costs associated with the Cost of Good Quality (CoGQ) and the Cost of Poor Quality (CoPQ). The CoGQ are expenses incurred to prevent, detect, and correct quality problems. The CoPQ, on the other hand, consists of expenses associated with the scrap, rework, and warranty work that results from quality problems.
Therefore, adding the CoGQ and CoPQ together will give you your total cost of quality.
COQ = CoGQ + CoPQ…. This is expanded below:
- The Cost of Good Quality is the sum total of Prevention Cost and Appraisal Cost (COGQ = PC + AC).
- The Cost of Poor Quality is the sum total of Internal and External Failure Costs (COPQ = IFC + EFC)
When you combine both equations, the Cost of Quality would look like this:
COQ = COGQ+ COPQ = (PC + AC) + (IFC + EFC).
{{banner-short-v2="/banner-ads"}}
Cost of good quality vs. the cost of bad quality
Cost of quality has four major components that can be categorized into “good” and “bad” quality.
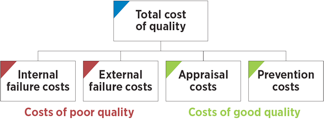
Combined together, the four main costs of quality make up the total cost of quality.
CoQ = (PC + AC) + (IFC + EFC).
Here,
- The cost of good quality is represented as CoGQ.
- The prevention cost is represented as a PC.
- AC represents the appraisal costs;
- IFC represents the internal failure costs.
- EFC represents the external failure costs.
🎓 Related reading: Use Automation to Maximize the P2P Cycle
Appraisal costs
Appraisal costs are incurred via measurement and inspection activities during operations to determine conformance to quality requirements. Therefore, it is performed before any product is delivered to the customer.
Examples of appraisal costs include:
- Test and inspections.
- Supplier acceptance sampling/supplier rating.
- Product audits.
- Calibration.
Prevention costs
Prevention costs are incurred to prevent or avoid quality problems. They are determined at the start of every new process step and are reputed for saving organized labor and manufacturing costs.
Therefore, if your business does not undertake prevention costs, you could experience high defect costs at a later stage, which could become too expensive for the business to handle.
Prevention costs are planned and designed before operations to guarantee good quality and prevent bad quality products or services.
Examples of prevention costs include:
- New product review.
- Quality planning.
- Supplier surveys.
- Procurement SOPs and process reviews.
- Quality improvement teams.
- Education and training.
- Conducting design reviews.
- Quality system audits.
- Process planning and control.
- Product modifications.
- Equipment upgrades.
Internal failure costs
are incurred to remedy defects discovered before the delivery of a product or service. These costs occur when the results of work fail to reach design quality standards and are detected before they are transferred to the customer.
Examples of internal failure costs are:
- Scrap: Defective products or materials that cannot be repaired, used, or sold.
- Rework/rectification: These are activities that include the correction of defective materials or errors.
- Waste: Performance of unnecessary work or holding of stock derived from miscommunication, a lack of SOPs, errors or disorganization.
- Failure analysis: Establishing the causes of internal product or service failure
- Re-inspection.
- Re-testing.
- Material review.
- Material downgrades.
- Design changes.
- Inventory required to support poor process yields and rejected lots.
External failure costs
External failure costs are expenses incurred to remedy defects discovered by customers after the customer receives the product or service. They occur when products or services that fail to reach design quality standards are not detected until after transfer to the customer.
Examples of external failure costs are:
- Processing customer complaints.
- Customer returns.
- Warranty claims.
- Product recalls.
- Sales returns and allowances
- Service level agreement penalties.
- Field service labor and parts costs incurred due to warranty obligations.
- Legal claims
- Lost customers and opportunities.
- Downgrading.
7 Examples of the classification of the cost of quality
Let's examine some examples to understand the types of cost of quality we identified above.
- The cost of quality-related training: This is a prevention cost since the essence of the training is to avoid or prevent poor quality.
- The cost of getting a company certified to ISO 9001: This is also a prevention cost, as its aim is to establish a system to avoid problems from happening in the first place.
- Review of drawings: This is an appraisal cost since you'll check to determine if the drawings have been made correctly.
- Product recall and warranty repairs: This is an external failure cost.
- Preparation of quality management system and inspection procedures: This is a prevention cost, as the quality management system and inspection procedures will help your business avoid quality problems.
- Inspection and re-inspection of the repaired product: These are internal failure costs.
- Defects found by customers after receiving the product: This is an external failure cost.
Why measure the cost of quality?
Measuring the cost of quality is important for helping businesses maintain a healthy and positive bottom line. Here's why businesses need to measure the cost of quality:
- Calculating the cost of quality (COQ) can help inform decisions as you balance investing in quality during the project and dealing with the future costs of failing to prevent or catch errors. These are known as costs of conformance and costs of non-conformance.
- Effective use and implementation of cost of quality methodology help your business to determine where to allocate resources to improve product quality and the bottom line.
- COQ helps a team determine whether its current quality control process meets customer expectations and what processes are causing a reduction in quality.
- Cost of quality helps in problem-solving, by performing cost and benefits analysis on quality and process improvement initiatives.
- The cost of quality methodology helps in a single-point evaluation of quality performance.
- It further evaluates the costs of failures and appraises them accordingly.
Difference between cost of quality & cost of poor quality
Below are some of the differences between both terms:
Cost of quality (COQ)
Cost of poor quality (CoPQ)
The cost of quality is determined by the CoGQ and CoPQ.
The cost of poor quality is a subset of the cost of quality.
The cost of quality is a methodology designed to help organizations determine the potential savings to be gained by implementing process improvements.
The CoPQ is the business cost incurred when defective products are identified before and after shipping to customers.
The cost of quality takes into account prevention costs, appraisal costs, internal failure costs, and external failure costs.
The sum of internal and external failure costs can be termed the CoPQ.
The prevention and appraisal costs do not constitute the CoPQ as such costs attempt to identify defective products at the beginning of the production process.
The CoPQ usually consists of product return costs and warranty costs related to the products.
The CoQ costs are incurred to prevent defects in products, or costs that are a result of defects in products. They aren't limited to the duration of a specific project — manufacturing.
.tg {border-collapse:collapse;border-spacing:0;}
.tg td{border-color:black;border-style:solid;border-width:1px;font-family:Arial, sans-serif;font-size:14px;
overflow:hidden;padding:10px 5px;word-break:normal;}
.tg th{border-color:black;border-style:solid;border-width:1px;font-family:Arial, sans-serif;font-size:14px;
font-weight:normal;overflow:hidden;padding:10px 5px;word-break:normal;}
.tg .tg-1wig{font-weight:bold;text-align:left;vertical-align:top}
.tg .tg-0lax{text-align:left;vertical-align:top}
Rather, they relate to all the activities from initial research and development (R & D) to customer service. Therefore, the complete product life-cycle (and not just the project life-cycle) is included while deriving the CoQ.
The CoPQ arises after the end of the production process and on defective finished goods.
5 Tips for reducing the cost of quality
Is it possible to reduce the cost of quality? Yes, even though the thought of it sounds daunting.
While it might look challenging to deliver high-quality solutions to customers while reducing overall CoQ and improving the bottom line — it's important to remember that the essence of reducing the CoQ is to prevent quality problems in the first place; as well as identifying and correcting them as quickly as possible when they do occur.
Here's how your company can reduce quality cost issues:
Improve training programs
Your employees can only operate maximally, alongside tools, resources and equipment if adequate training is provided. Therefore, the training should not only focus on quality standards and procedures but also be offered to both new and experienced employees.
Develop a culture of quality
Organizations, including yours, should develop a culture of quality from top to bottom.
Creating a quality culture will ensure that every aspect of the business is quality-driven, from products and services to employee treatment.
Invest in quality control
Quality control is the process of ensuring that products or services meet quality standards; via various methods such as inspections, testing and audits.
Ensure your company invests in quality control measures to prevent huge problems from happening. You'll enjoy long-term cost reduction benefits accrued from preventing scrap, rework, and warranty work.
Use quality tools and methodologies
Numerous tools and methodologies like Six Sigma, Lean, and the Deming Cycle help businesses improve their product or service quality. Additionally, they help to identify and correct quality problems and aid the continuous improvement of processes.
Invest in software that enhances quality
Quality software can help your business automate quality control processes and ultimately improve team collaboration, productivity, employee communication and employee training.
Take Standard operating procedures (SOPs) for example. SOPs are one of the best ways to reduce quality costs. They help you share knowledge and ensure repeatable, high-quality results. These standards increase safety and efficiency and also save you money.
This type of knowledge base is designed to build standard processes, resulting in quality output — while enabling rapid knowledge transfer and training. Additionally, they offer the following benefits:
SOPs are important for increasing efficiency, reducing errors and improving quality by defining a “way” of doing things. Hence, they're one of the best go-to strategies for achieving quality and consistency.
Well-documented SOPs can help reduce a new employee's learning curve or training time. By referring to the SOP, a new or existing employee can easily refer to a document to get them up to speed quickly, saving time and money.
SOPs enable the easy replication of processes across your company — across different regions, or to embed a newly acquired business.
Scribe is your best bet if you're looking to reduce the cost of quality by creating SOPs. Scribe is a cloud-based knowledge management software that allows you to capture, organize and share your established knowledge. Your employees and customers can use the knowledge base internally or externally.
Scribe lets you edit SOPs by adding rich content and media — including screen recordings, videos, images, or charts. You can also easily collaborate with team members and other important stakeholders — plus, it serves as a base for centralized information. You can create policies and procedure manuals and easily locate and access SOPs when they are needed (in one central database).
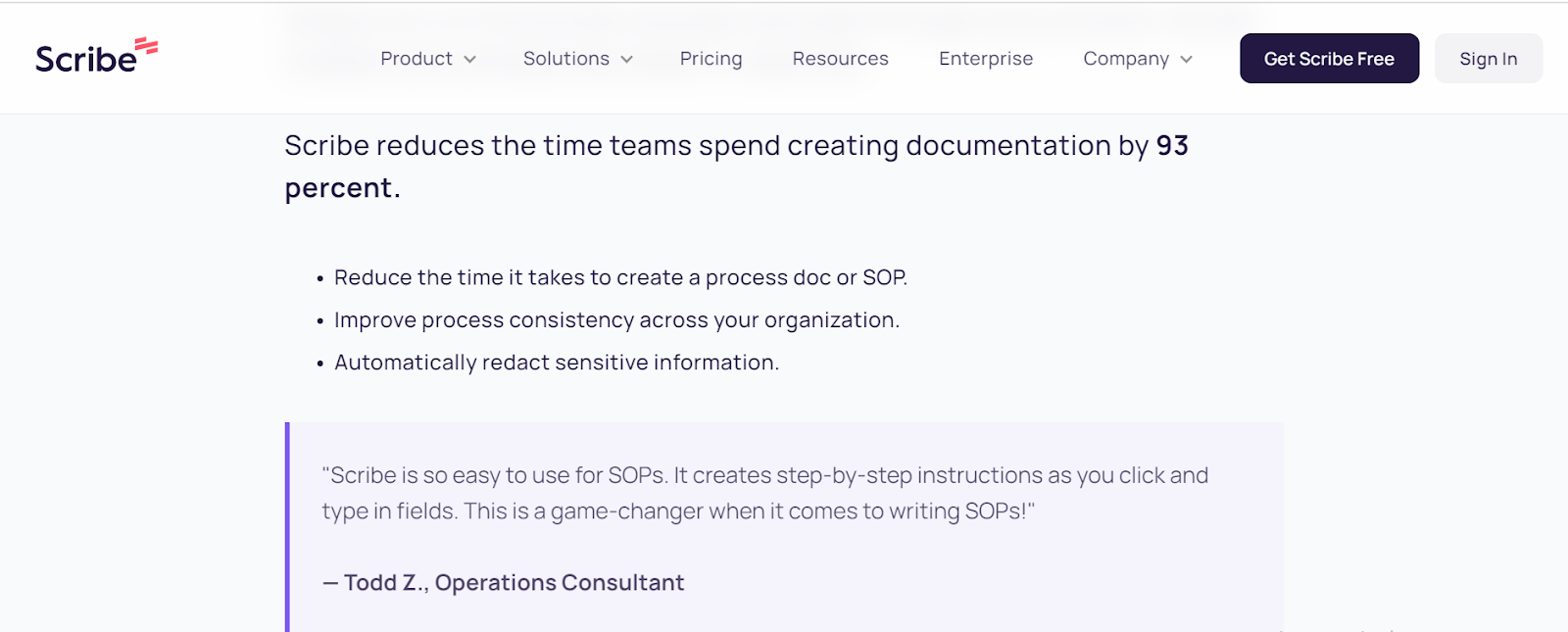
Here are some of the reasons why you should sign up on Scribe today:
- Automates documentation.
- No coding is required as it's easy to set up.
- Scribe is ideal for any company looking to record its documentation online since it includes features like user access controls, performance tracking, customization, and styling tools.
- Its strong security features protect your valuable SOP information.
- Access to free SOP templates that ensures you don't have to create operations policies and frameworks from scratch.
- Scribe includes compliance sign-off and authorization features.
- Allows you to create custom workflows and procedure documentation to match their specific needs.
- Managers can add members to their teams, define subjects, and assign roles.
- It allows for color and logo modification.
- Text, steps, and images can all be easily customized.
- Simple to integrate into any knowledge base or other favourite tools.
- Allows you to share with anyone, anywhere via different formats with one single click!
Not convinced yet?
Check out these reviews from some of our users on G2! 😁
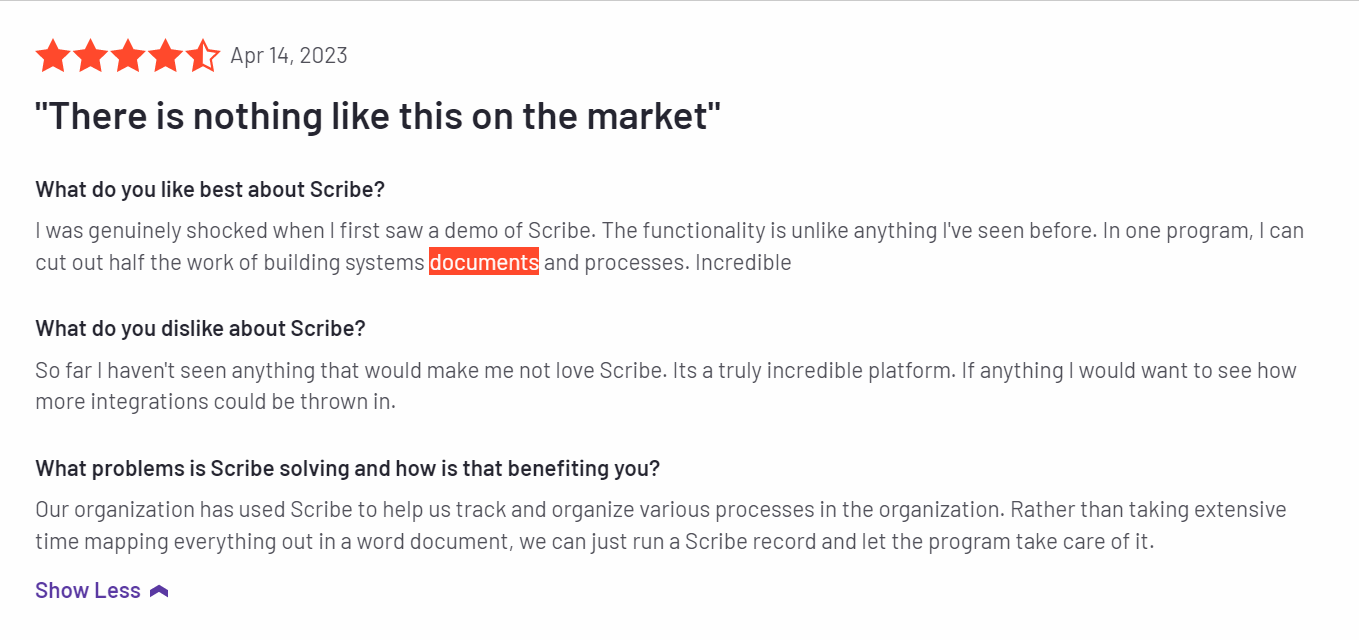

So, what are you waiting for? 😉 Sign up for free and create your process document in seconds!