Introduction
Organizations constantly strive to improve efficiency and productivity. One approach that has gained popularity is standard work, a Lean manufacturing concept that aims to create a consistent and streamlined process for completing tasks.
While standard work is commonly associated with manufacturing environments, it can also be applied to office settings to optimize workflow and enhance overall performance.
A standard work template is a step-by-step guide that can easily be transferred to anyone in your organization—with the sole aim of guiding them in carrying out their daily responsibilities, especially when there is no one to monitor them.
In this blog post, we'll explore how to write a standard work template and best practices for your organization. Dive in!
Standard work template takeaways:
- Standard work instructions provide detailed guidelines for employees to work faster and execute tasks correctly.
- A standard work template is a step-by-step guide that can be easily transferred to anyone in the organization.
- A standard work template reduces errors, saves time, builds an internal knowledge base, and improves employee onboarding and training.
- To write an effective standard work template, include a clear title, descriptive introduction, purpose of the task, detailed instructions, proper formatting, information validation, and references.
Use AI to create standard work templates in seconds ➜
What is standard work?
Standard work is a systematic approach to defining, documenting and implementing the best practices for performing a work process. It is a core principle of Lean manufacturing, and it can be applied to any type of process, from manufacturing to office work.
Standard work is the best-known and demonstrated method for producing a product or service. It's essentially a recipe for success.
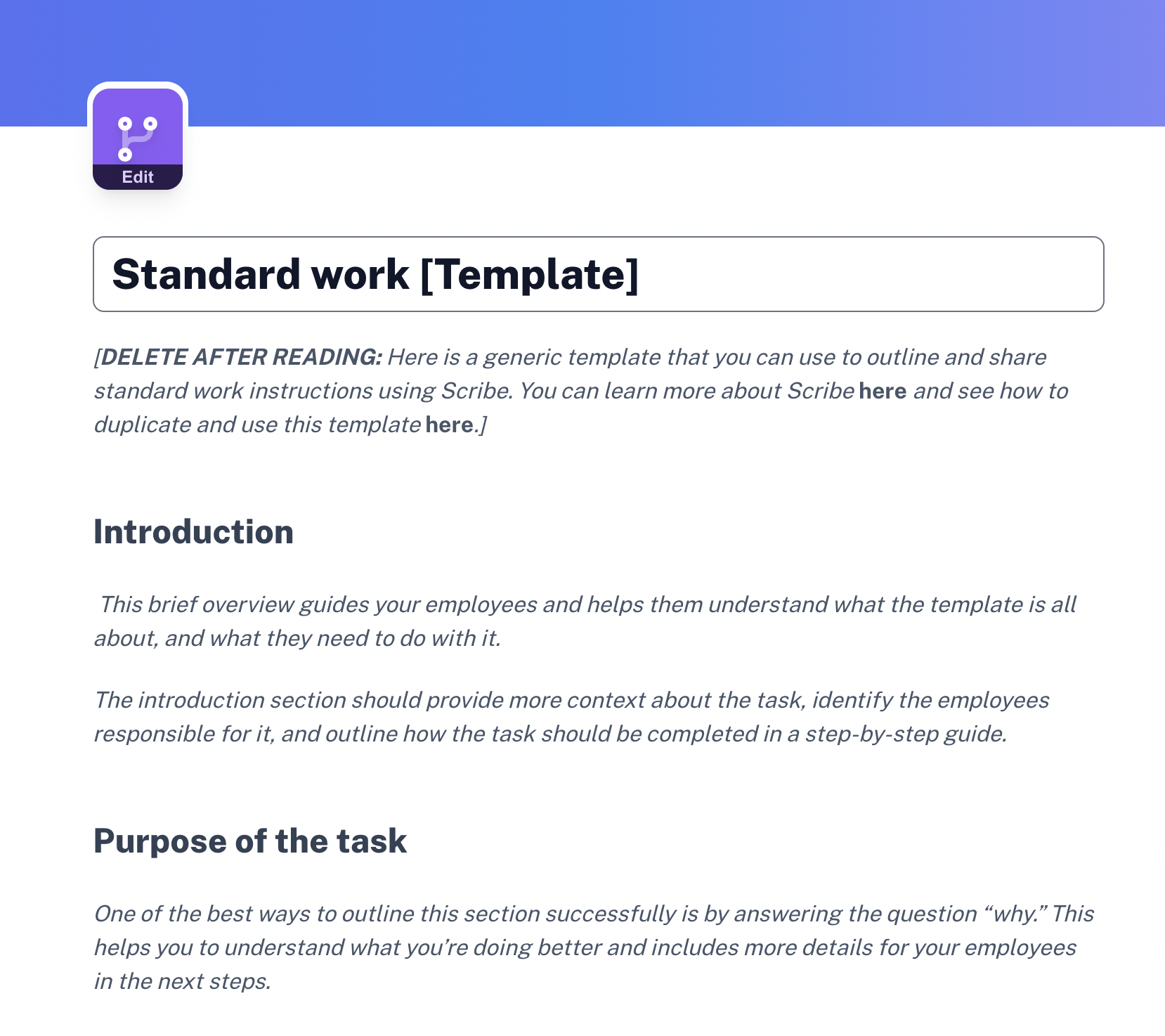
What are the 4 elements of standard work?
Standard work is designed to create consistency and efficiency in processes. There are four essential elements of standard work that help to achieve these goals.
- Takt time is the rate at which a product or service needs to be completed in order to meet customer demand. It's calculated by dividing the available production time by the customer demand. Takt time sets the pace for the work and ensures that it is completed in a timely manner.
- The standardized work sequence outlines the specific steps and order in which tasks should be performed. It provides a clear roadmap for employees to follow and ensures that work is done consistently and efficiently.
- Standard in-process stock is the amount of inventory that should be present at each step of the process. It helps to prevent bottlenecks and ensures that work can flow smoothly from one step to the next.
- Standard work-in-progress refers to the maximum amount of work that should be in progress at any given time. It helps to prevent overproduction and ensures that resources are not wasted on unnecessary work.
Once these elements have been defined, standard work can be documented using a variety of tools, such as process mapping, work instructions and standard operating procedures.
{{banner-short-v2="/banner-ads"}}
What are standard work examples?
A clear example of standardized work could be machine operations in the Production department. It may mean employees must follow an operation and maintenance manual to operate certain machinery correctly and safely.
Another example is utilizing standard work instructions in customer-facing roles. Customer support employees are usually given scripts for specific customer service encounters. In turn, this establishes specific replies and approaches in different customer service situations—without compromising uniformity.
Create standard work templates for free with Scribe ➜
How to write a standard work template
A standard work template should achieve three major things: be clear, useful and helpful. Below is an outline of a standard work template, plus some standard work tips on how to make it effective.
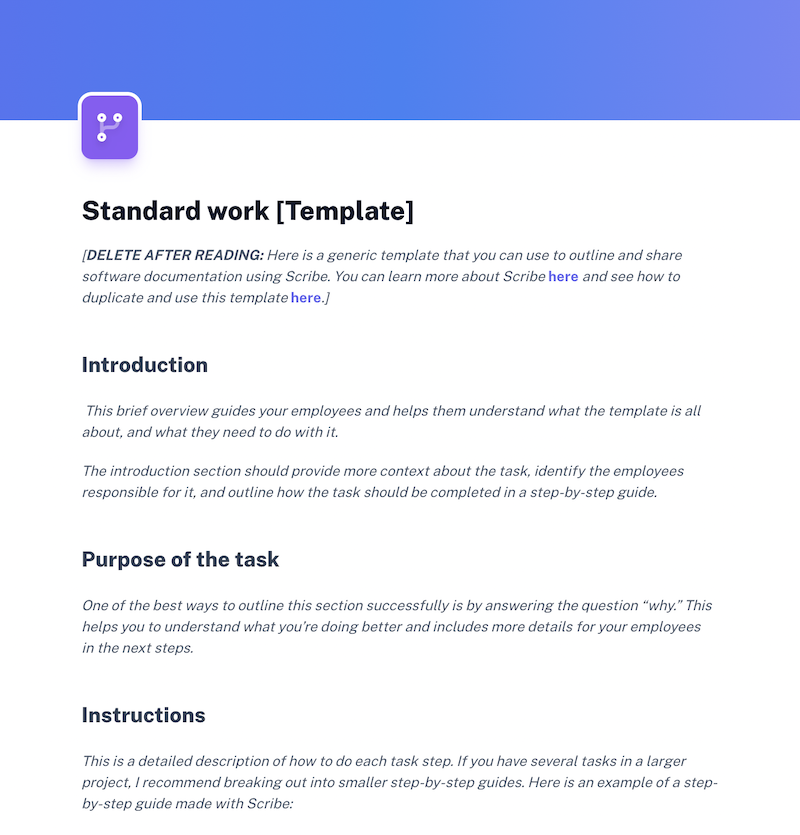
Here's a free standard work template you can use and share today.
1. Select a process to standardize
This could be a manufacturing process, an office process, or any other type of process that is performed on a regular basis.
2. Break the process down into individual steps
Once you have a good understanding of the process, break it down into the individual steps that are required to complete it.
Now you're ready to document the standard work process and create your template.
3. Use a clear & easy-to-understand title
Ensure that the title is clear and easy to understand.
The title is the first thing anybody reading the template will see. Since the work instruction template shows your employees how to accomplish a task, one of the best headline formats for this is the “How To” format. An example is “How To Fix a Rechargeable Fan's 12V DC Motor."
4. Add a descriptive introduction
The next step when writing a standard work template outline is to include a descriptive introduction. This guides your employees and helps them understand what the template is all about, and what they need to do with it.
The introduction section should provide more context about the task, identify the employees responsible for it, and outline how the task should be completed in a step-by-step guide.
Using the example, “How To Fix a Rechargeable Fan's 12V DC Motor," a short introduction could be:
“This standard work template shows you how to fix a rechargeable fan's 12V DC motor in the company. Team members in the production/technical department should use this guide whenever there’s a need to fix the DC motor of a rechargeable fan in the organization."
Here's an example of what a Scribe Page for “How To Fix a Rechargeable Fan's 12V DC Motor" looks like:
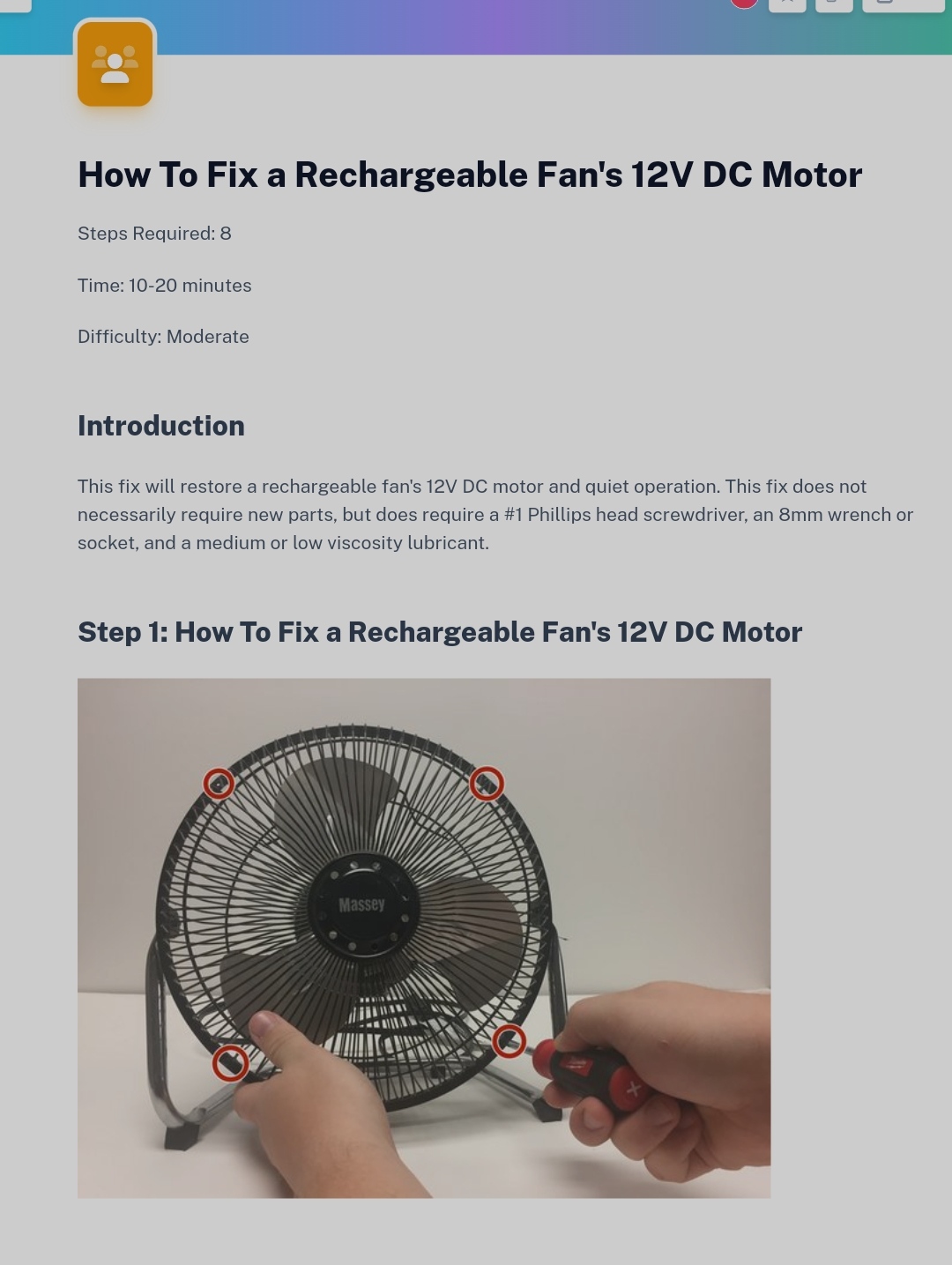
Create standard work templates in seconds with Scribe ➜
5. Describe the purpose
Include the reason(s) for creating a standard work template for your Product/Production teams in this section. Doing this helps you identify its purpose in the first place.
One of the best ways to do this successfully is by answering the question “why.” This helps you to understand what you’re doing better and includes more details for your employees in the next steps.
Still using the “How To Fix a Rechargeable Fan's 12V DC Motor" example, your "whys" could be:
- Why should you fix a rechargeable fan's 12V DC motor?
- Why is fixing a rechargeable fan's 12V DC motor important?
- What steps should you take to fix a rechargeable fan's 12V DC motor?
- Who should be responsible for fixing a rechargeable fan's 12V DC motor?
6. Document each step in detail
This includes describing the key tasks, materials and equipment required, and the quality standards that need to be met.
If you don’t show your new employees how to complete a task or use a product, chances are they won’t know how to do it. And that's why this is the most critical section in a standard work template.
The first thing you should do is to mention all the materials needed to complete a task. In the case of repairing a rechargeable fan's 12V DC motor, some of the materials needed to complete the task include:
- Scraping pliers.
- Alligator clip (KKL type).
- Round steel tube brush (SCOC type).
- Flat steel tube brush (SCOR type).
- Bending tool.
- Stripping insert.
7. Sequence the steps in the order that they are performed
The next step is to break down how to complete each task in an easy-to-follow direction that is clear and understandable.
Break down complex tasks into smaller, more manageable steps.
Where applicable, use diagrams, images, videos, and charts to explain this step better.
Be sure to estimate the cycle time for each step, which is the amount of time it should take to complete the step under normal conditions.
8. Identify the potential hazards associated with each step
This includes identifying both physical and safety hazards.
Develop safety precautions for each step to reduce the risk of accidents and injuries.
9. Use consistent formatting
Formatting ensures that your standard work template is easy to read and understand. Here are some tips:
- Use images where possible.
- Bold each step so that it stands out.
- Use heading tags to ensure that the title and subtitles stand out.
- Include numbered and bulleted items.
- Make sure the instructions are arranged sequentially.
- Use color filters where necessary.
10. Add references
Where necessary, add references at the end of your standard work template. This means either adding an appendix or footnotes at the end of the template. Adding references provides your employees with more sources that they can visit for further reading.
11. Validate your instructions
Once you’ve completed all the steps above, the next thing to do is validate the information. Reach out to key stakeholders in the company, especially experienced employees, who have a firm grasp of the workings of each department.
Also, you can consult subject matter experts to verify if all the steps in the instructions are current and accurate.
12. Train employees on your standard work template
Once your new standard work template is developed, it is important to implement it and train employees on it. This will help to ensure that the process is performed consistently and efficiently.
13. Monitor and evaluate your standard work template
Monitor and evaluate the standard work template on a regular basis to ensure that it's effective and employees are following it. Identify any areas for improvement and improve as needed.
Kaizen: continuously improving standard work templates
Kaizen and standard work are two closely related concepts in Lean manufacturing. Standard work is the foundation for kaizen because it provides a baseline against which to measure improvements.
Kaizen is a Japanese term meaning "continuous improvement" or "change for the better." Kaizen is the process of continuously improving standard work. This involves identifying and eliminating waste, streamlining the process, and making other incremental improvements.
The goal of kaizen is to create a culture of continuous improvement, where employees are encouraged to identify and suggest ways to make their work more efficient and effective.
Here are some tips on how to apply kaizen when creating a standard work template:
- Eliminate unnecessary steps. If a step in the process does not add value, it should be eliminated or combined into a single step.
- Streamline the process. Look for ways to reduce the amount of time and effort required to complete the process.
- Improve quality control. Identify and eliminate the root causes of defects, and look for ways to prevent that defect from occurring in the first place.
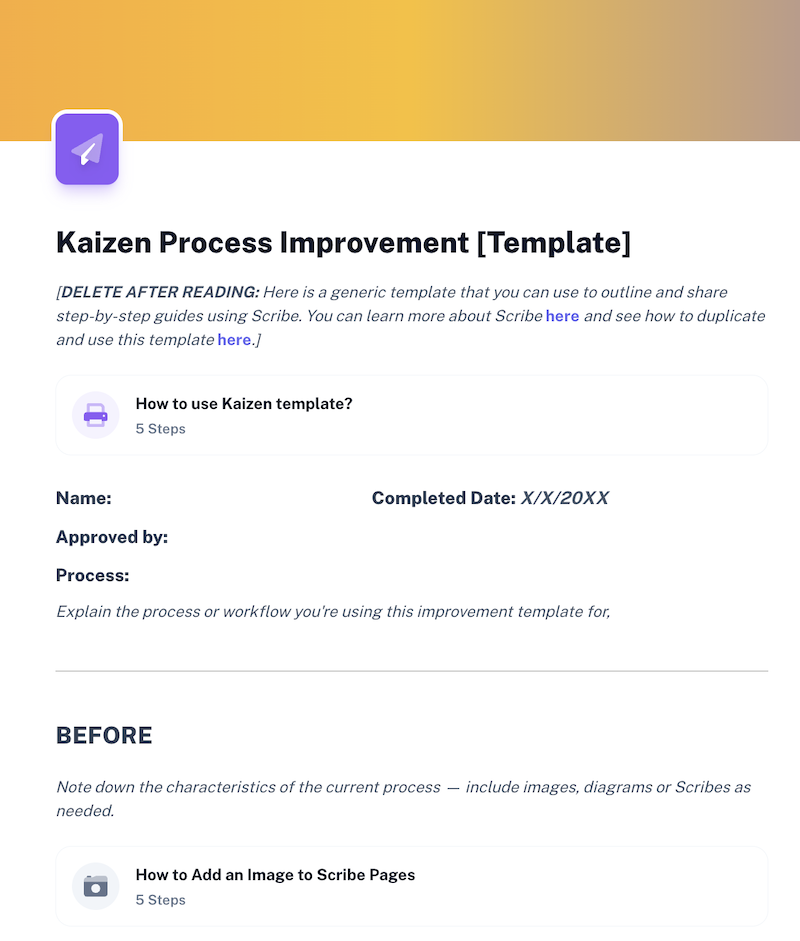
By implementing standard work and continuously improving it through kaizen, you can achieve significant improvements in efficiency, quality, safety and cost.
What are the benefits of a standard work template?
Some of the uses of this documentation include the following:
- Ensures that every employee abides with the regulatory standards.
- Outlines how employees can perform complex tasks.
- Eliminates communication barriers.
- Implements a consistent method for projects and best practices.
- Explains what each part of a process or task in the company entails, such as the tools, responsibilities, requirements, etc.
- Helps train new employees, informs the employee handbook and updates established employees on company processes and procedures.
Build standard work instructions in seconds with Scribe ➜
FAQs
What is a standard work sheet?
A standard work sheet, also known as a standard work template, outlines the steps and procedures required to complete a specific task or process.
- A standard work sheet is a guide for employees to follow for consistency and efficiency in their work.
- It establishes standardized methods for tasks, improving productivity and reducing errors.
- A standard work sheet includes detailed instructions, time estimates, visual aids, safety precautions, quality standards, and key performance indicators.
What are the 4 types of standard work?
Standard work refers to the documented and agreed-upon best practices for completing a specific task or process. The four common types of standard work are:
- Standardized work focuses on creating a consistent and repeatable process, includes detailed instructions, eliminates variations, and improves quality and efficiency.
- Standard work combination sheet: Combines multiple tasks into a single document, provides a visual representation of sequence and timing, identifies opportunities for improvement, and ensures efficient task performance.
- Standard work in process focuses on managing the flow of work, includes guidelines on work quantity, handling bottlenecks and workload balance, prevents overproduction, reduces lead times, and improves process flow.
- Standard work for leaders: Specific to leaders, supervisors and managers, it includes guidelines on managing and supporting the team, conducting gemba walks, providing coaching and feedback, and supporting continuous improvement at the operational level.
💡 Save time and streamline your processes with Scribe's free operational level agreement template.
What's the difference between standard work and Standard Operating Procedures?
Standard work refers to documented best practices and processes for a specific task, ensuring consistency and efficiency.
Standard operating procedures (SOPs) provide a broader framework for an organization's operations.
- Standard work is often a component of SOPs, providing detailed instructions for specific tasks within the broader framework.
- SOPs outline policies, processes, and guidelines in human resources, finance, customer service, and safety.
Conclusion
Creating standard work templates can significantly improve efficiency, productivity and overall performance.
By leveraging insights from Lean manufacturing experts, your organization can create a culture of standardization and continuous improvement, driving sustainable growth and success.
Ready to create your next standard work template for free? Sign up for Scribe today and get started!