Introduction
Does your team go into a state of chaos every time a machine breaks down? Or does your maintenance staff struggle to carry out routine tasks seamlessly?
These are clear signs that you need an operation and maintenance (O&M) manual.
An O&M manual consolidates detailed information about your organization and facility — from routine processes to emergency emergency procedures — to streamline operations and maximize efficiency.
I’ll break down what an operation and maintenance manual is, what it includes and why you need one.
I’ll also walk through the tried-and-tested steps for building your own manual and free templates to get started in a snap.
TL;DR: Operation and maintenance manual
- O&M meaning: An operation and maintenance manual is a detailed document for equipment upkeep in companies.
- It includes an overview, operation instructions, maintenance instructions, and emergency protocols.
- Benefits include preparedness, centralized information, quality performance, onboarding assistance, and safety standards.
- Creating a manual involves planning, feedback, and continuous updating.
What is an operation and maintenance manual?
An operation and maintenance manual documents essential, detailed information about an organization, typically a manufacturing unit. This instruction manual covers day-to-day operations such as equipment upkeep, facility and inventory management, maintenance processes, SOPs, and more.
A good O&M manual can:
- Reduce downtime or unplanned shutdowns.
- Lower maintenance expenditure.
- Extend the life cycle of machinery.
- Build alignment within the team.
- Improve safety.
Put simply, O&M manuals turn chaos into order to enhance your operational efficiency and drive higher ROI.
But now, the bigger question is: what exactly goes into an operation & maintenance manual?
Let’s dive deep into the main components of this manual.
Key components of an operation and maintenance manual
Here’s what you should include in your operations manual template:
- Company overview: A concise overview of the company to contextualize the manual’s goals. Think of this section as a quick introduction to new hires or third-party vendors.
- Maintenance SOPs: Detailed information and step-by-step instructions for performing routine equipment and factory or facility maintenance tasks. Well-documented SOPs can help your maintenance team perform regular maintenance checks and prevent equipment failure or emergencies.
- Operational instructions: Clear instructions for operating different machines or systems. It also includes guidelines for dealing with accidents and steps to prevent mistakes.
- Property or facility details: Valuable information about your physical property—like facility layouts and infrastructure details. Use this information to plan maintenance work, streamline daily operations, and inform new hires about the location.
- Illustrations and diagrams: Visual diagrams of all equipment and graphic representations of different processes, like drawings, schematic diagrams, photos and other assets to simplify complex information.
- Emergency protocols and safety guidelines: Break down multiple plans of action for dealing with emergency situations. It also covers general safety guidelines to avoid a potential mishap and ensure the well-being of all staff at your facility.
While these are a few standard components in all O&M manuals, you can also create different types of manuals to drive operational improvement.
Let’s look at the most common examples you might want to create.
📌 Related resource: Operations Manual: What it is & How to Write it (+ Free Template)
Types of operation and maintenance manuals
Here are the most commonly used O&M manuals:
- User manuals: These user guides provide instructions for using a particular machine, tool or software. They’re comprehensive documents with guidance for assembly, usage, maintenance, and repair.
- Safety manuals: These manuals are specifically created for identifying hazards and implementing safety procedures. They come in handy during an emergency situation but also help in educating workers about equipment handling.
- Maintenance manuals: These manuals include SOPs for routine maintenance tasks and timelines. They give you a breakdown of different steps and activities for regular checkups to maximize equipment efficiency.
- Recovery & backup manuals: These manuals provide the steps to recover data lost during a server outage or cyber-attack. They’re more relevant for IT operations management and highlight the steps for recovering lost data and creating a backup.
- Product installation manuals: These manuals give you a step-by-step guide for installing a product or assembling a machine. They also share instructions to get started and how to use different functions.
Now that we’ve understood what O&M manuals are, let’s look at key reasons why you should create one for your organization.
5 key benefits of operation and maintenance manuals
As your organization grows, operations management expands with it — more equipment, a bigger workforce and more operational processes to scale production. An O&M manual can support your growth by acting as a single source of truth to eliminate all inefficiencies.
But this manual isn’t just for large teams or high-growth companies. Even lean teams need O&M manuals to streamline processes.
Let’s look at a few critical benefits of creating an operation and maintenance manual.
1. Simplifies employee training
By documenting everything about your organization, you essentially create a full-fledged roadmap for new employees to navigate life within your organization.
It’s a comprehensive, valuable resource for new hires to get up to speed much faster.
Plus, this manual becomes a reliable source employees can refer to whenever they need answers or instructions.
2. Improves workforce safety
Believe it or not, safety is the most definitive factor driving your business’s growth.
Without a safe working environment, you’re bound to face repeat accidents, employee attrition and lower production yield.
An operations & maintenance manual reiterates the safety protocols to:
- Prevent accidents and errors leading to emergencies.
- Proactively assess an emergency situation and implement solutions.
This manual can educate new hires and employees on machine operating procedures and avoiding unsafe practices.
3. Helps in troubleshooting
O&M manuals can also fast-track resolution for any problem, like a system or equipment failure.
Instead of wasting time on a trial-and-error approach, an operations manual can reduce downtime and clearly outline possible causes behind the problem.
It’ll also provide methods to troubleshoot issues and minimize the impact on your overall productivity.
4. Ensures consistent operations
An operations manual can standardize operating procedures and build consistency across the board.
Even if you’re working with a remote or distributed team, you can ensure uniformity in daily operations through properly documented SOPs.
Besides making operations more consistent, these SOPs can also help in quality control and reduce costly mistakes.
5. Cuts down operational costs
You can save operational costs with an O&M manual in so many ways. For starters, your employees and new hires have the knowledge and skills to correctly operate all equipment.
This will inevitably reduce accidents or damage and minimize expenses on fixing wear and tear.
You can also reduce the overall interruptions and delays in business operations. This means, your team works with greater efficiency and produces more output.
How to write an operation and maintenance manual
Let’s answer the million-dollar question: how exactly should you create an operations and maintenance manual?
I analyzed dozens of O&M manuals and templates to find these six tips for creating one.
1. Define your O&M manual’s structure
First things first, you have to decide how you want to organize your manual. Like building a Lego set, you need a big-picture structure to clearly consolidate the many moving parts in your business operations.
Start with the basics to prepare the groundwork — the company overview, guidelines on how to use this manual, equipment descriptions, drawings, and more.
Once you’ve done the initial legwork, you’ll have a detailed layout to structure your manual. And you’ll also have the detailed information to guide the next steps.
Remember to write explanatory headings for each section to avoid any confusion.
💡 Pro tip: Consider the target audience for your manual (employees and contractors). Then, assess your manual’s structure from their perspective and make necessary changes to make the information easily understandable to them.
2. Set up creation and approval workflows
Building an O&M manual for your entire business isn’t a one-person effort or a one-and-done process. You'll be working with a team for the long term and updating the manual to make iterations in the future.
Build a workflow to create different parts of the manual and assign ownership to the right stakeholders to execute this workflow.
Here are a few tips to achieve this:
- Finalize your team: Decide the key contributors to the O&M manual. You have to define two kinds of stakeholders in your team—those who will own parts of the manual and those who will provide inputs for maintaining accuracy. Document and share this important information with everyone to keep them on the same page.
- Visualize the workflow: Remember to visualize this entire chain of events when you’ve created an end-to-end workflow—from collecting suggestions to making edits to rolling out the document. This makes it easier for all parties to track progress and be aware of the next steps.
- Allocate responsibilities: While building your workflow, you should also assign owners for every task and present a set of responsibilities. For example, if Person A is responsible for creating SOPs, then you should give them a list of action items to complete for completing all SOPs.
Lastly, be sure to schedule progress check-ins for every team member to complete their tasks within the defined timeline.
A good project management tool like Notion or Asana can make this entire process seamless for your team.
3. Collect inputs from relevant stakeholders
It’s time to dig in and start collecting the necessary information, suggestions or insights from the right people.
For example, if you’re creating a guide on weekly maintenance tasks for your facility, ask for suggestions from the people responsible for the routine maintenance of different machines in your company.
While this step looks easy on the surface, it can become overwhelming if you don’t move strategically.
As a best practice, you should roll out surveys to gather valuable information from subject matter experts. You can also schedule interviews if you’re working on a complex topic.
The goal is to collect meaningful insights and make this information easily accessible to your target audience.
4. Use a seamless documentation tool
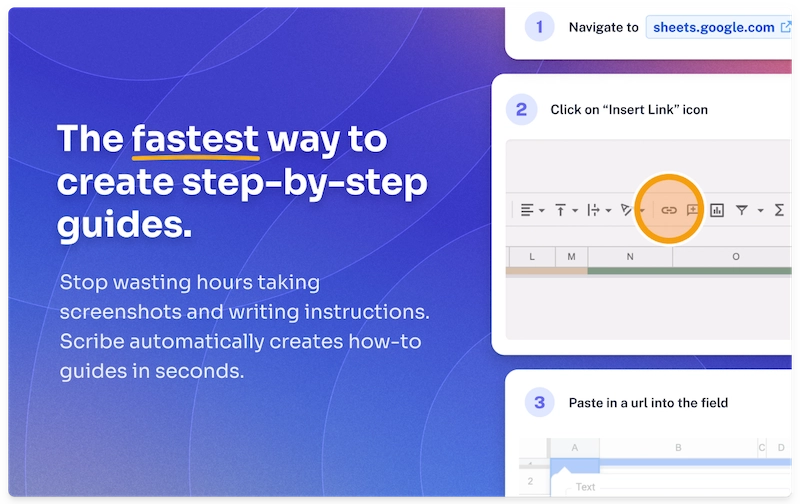
Once you’ve collected all the data, it’s time to get cooking!
You can create detailed SOPs and specialized manuals with a visual documentation tool like Scribe.
Scribe captures knowledge in seconds and converts it into step-by-step guides packed with annotated screenshots, instructional text, media and links. Simply capture your screen while performing a task and Scribe will automatically generate a visually appealing guide for this process.
Here’s a quick look at a Scribe one of our users created on how to use a telematics dispatch schedule dashboard:
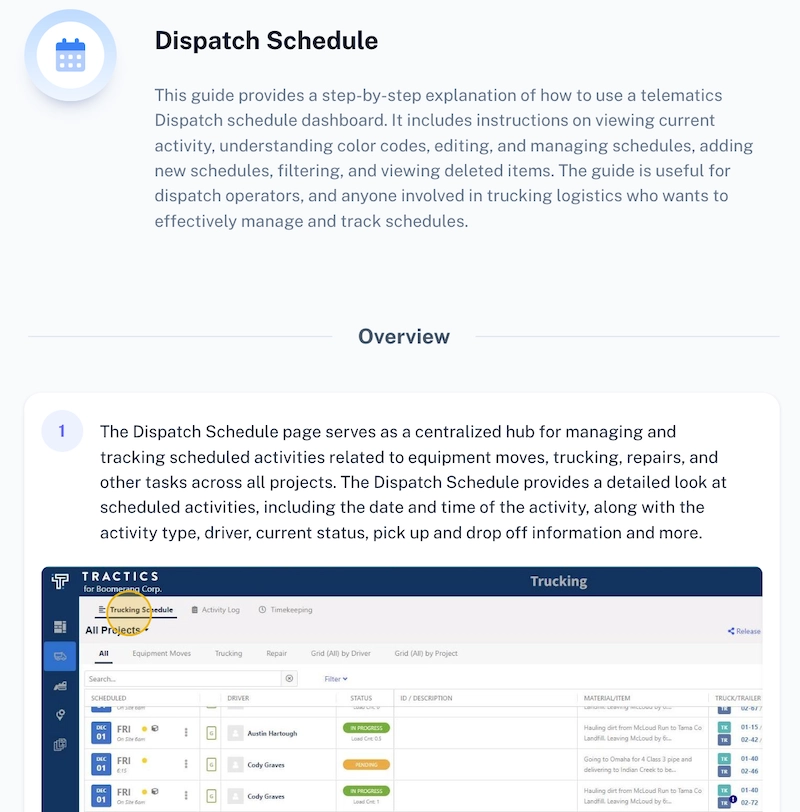
And there’s more! Besides creating SOPs for specific tasks or instructions for operational activities, you can also make a full-fledged O&M manual with Pages.
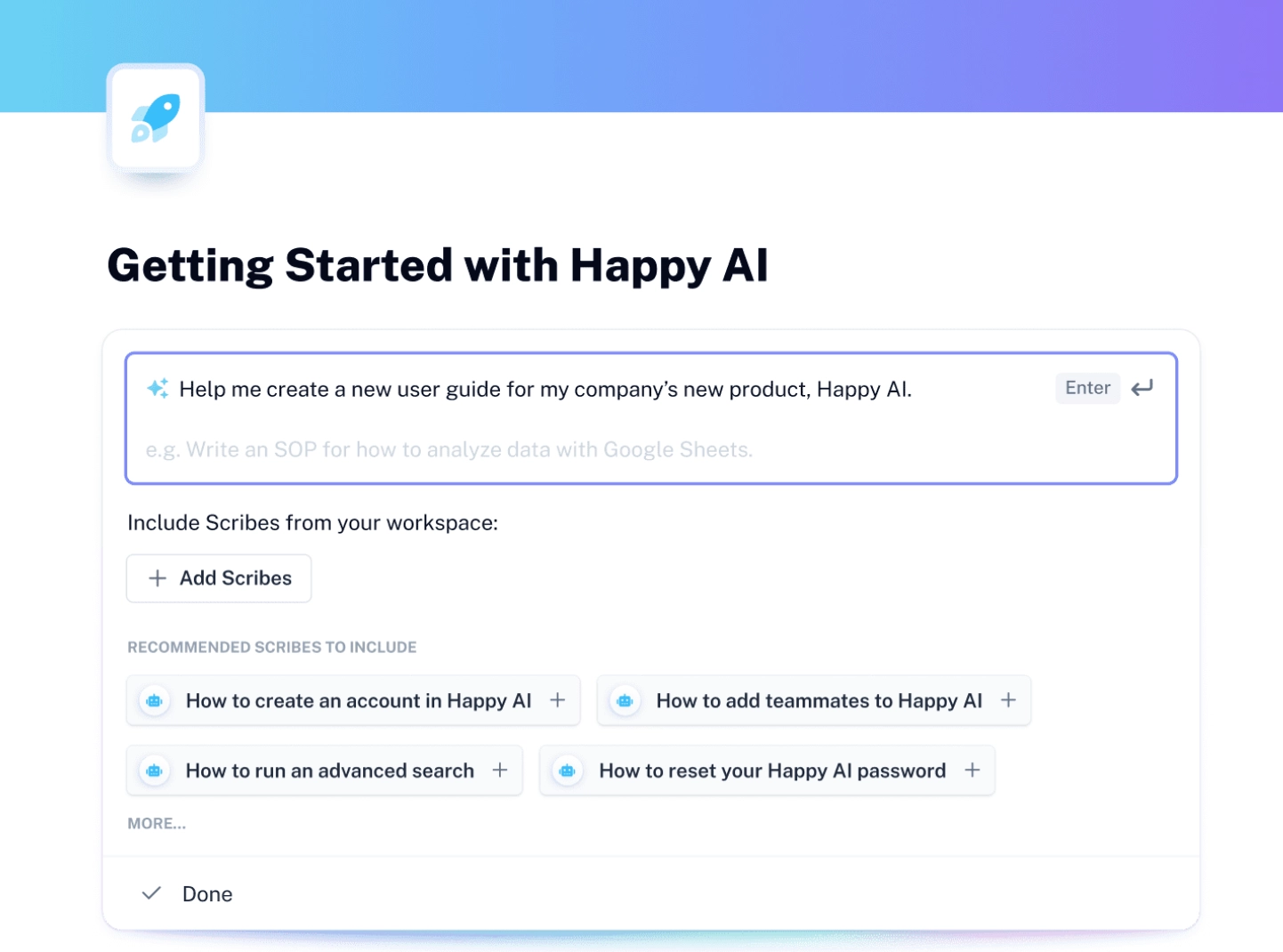
Pages lets you add multiple Scribes in one place along with detailed text, images, videos and other elements.
You can format this document any way you like and share the digital manual with a single link or export it to PDF for a hard copy O&M manual.
Knowledge-sharing has never been easier—Josie, a Scribe user, agrees:
“Previously, I was spending hours in my operations role documenting long and complicated digital processes. Due to the manual nature of this, it was very common for steps to be missed. Scribe has totally solved this issue. I'm winning back multiple hours a week and the guides look so much better than our previous SOP template.”
5. Add visuals and interactive elements
In addition to creating SOPs with Scribe, you can add some visual elements to your first draft to make it more engaging to your target audience.
Visual aids enhance your manual’s readability and improve information retrieval. Plus, it’s easier for people to see the solution than reading text blocks.
Besides visuals, you can also add interactive elements, like:
- Clickable links.
- Search functionality.
- Interactive checklists.
- Self-serve interactive demos.
Creating a level of interactivity can make readers more invested in this manual. They’ll understand relevant information when it's engaging.
6. Get feedback and iterate accordingly
When you’re ready with the first draft, you can soft-launch it to a small group of employees and collect feedback.
This step is crucial to identify any gaps and opportunities to improve your manual and make it more comprehensive.
Once you’ve implemented changes to your first draft based on this user feedback, you’re all set to roll the final draft out to the entire org. Remember to make the manual easily shareable and accessible for everyone.
Don't forget to establish a regular review and update process to proactively identify any areas needing updates.
Make sure you keep reviewing and updating your manuals on a regular basis. This proactive approach will help you identify any areas that may need some updates.
📌 Related resource: Procedures vs. Work Instructions and why you need both.
Get ready-to-use O&M manual templates!
Here are a few free templates to help you build a detailed O&M manual in minutes.
Operation and maintenance manual template
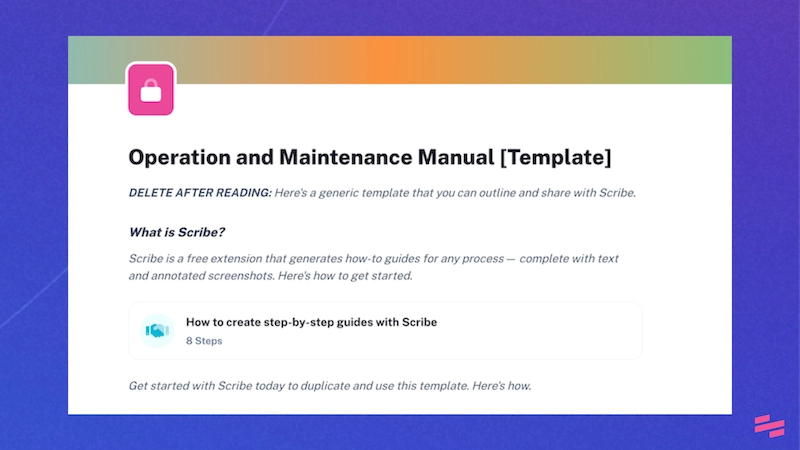
Use this operation and maintenance manual template to create a manual with:
- An overview of your company history, organizational chart, and employee information.
- Facility or property details such as floor plans, building code and materials.
- Maintenance approaches including procedures, responsibilities, schedules, and troubleshooting processes.
- Emergency procedures for crisis mode.
👉 Try this operation and maintenance manual template for free.
Standard Operating Procedure (SOP) template
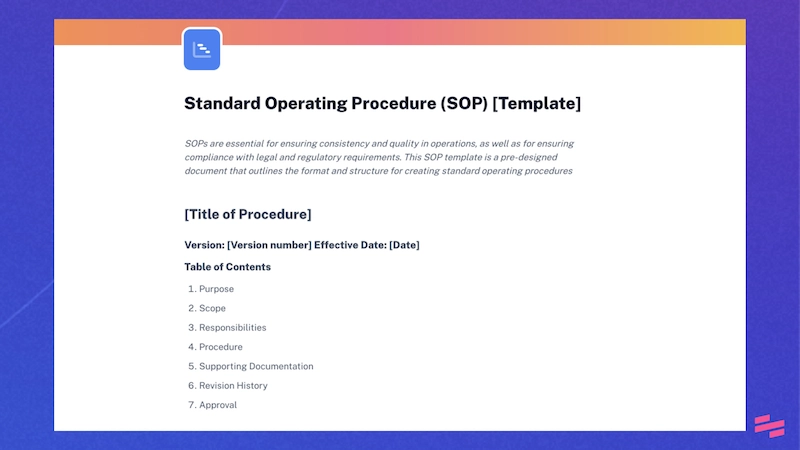
Use this customizable Standard Operating Procedure (SOP) template to create step-by-step instructions for common tasks. Here are just a few ways you can document procedures:
Machine operating procedures:
- Startup and shutdown: Detail the proper steps to initiate and conclude operations safely and efficiently.
- Normal operating ranges: Ideal parameters for operating equipment.
- Procedures for handling situations outside the normal operating range.
Maintenance procedures:
- Routine maintenance schedule: A structured plan for preventative maintenance, including frequency and specific actions for each task.
- Calibration procedures: Detailed information on how to calibrate instruments and equipment for optimal functioning.
- Parts replacement instructions: Instructions on how to safely replace components.
Safety procedures:
- General safety guidelines: Safe work practices around equipment.
- Emergency response procedures: Steps to take in case of accidents, fires or other emergencies in your facility, including contact information for relevant personnel and agencies.
👉 Try this Standard Operating Procedure template for free.
Safety work instructions
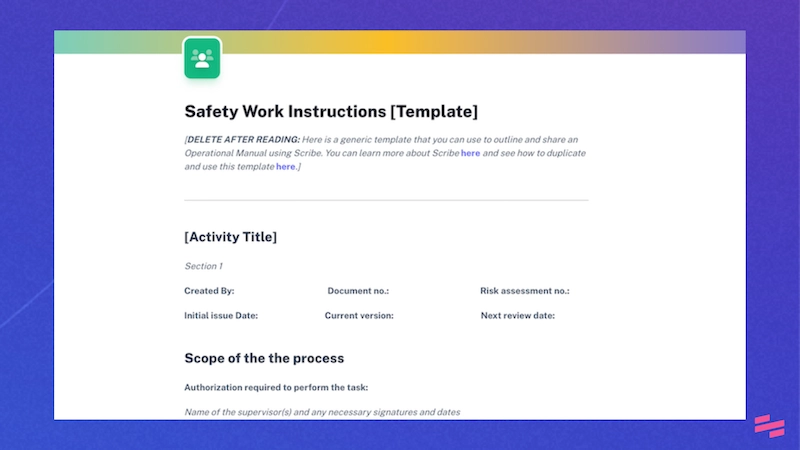
Use this safety work instructions template to build safety guidelines and maintain safety standards in your facility.
- Step-by-step instructions for tasks with hazards and safety controls.
- Potential hazards and preventative actions.
- Emergency protocols, follow-up instructions, authorization requirements, and more.
👉 Try this safety work instructions template for free.
Construction site work instruction template
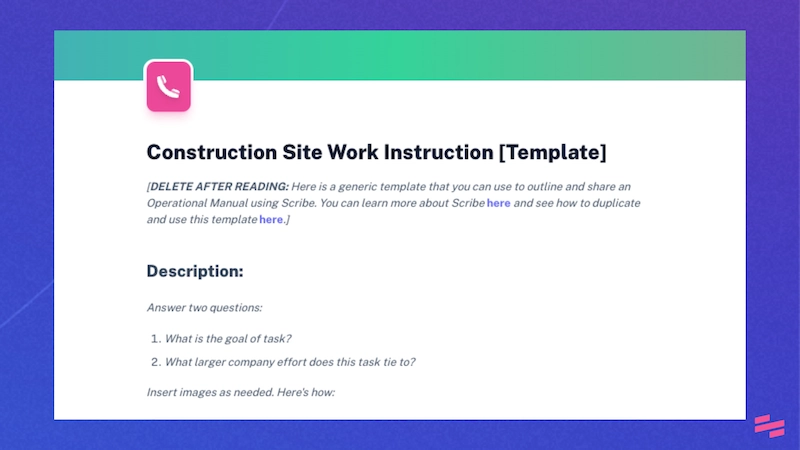
If you're in the construction industry, use this template to build detailed, step-by-step procedures to:
- Ensure consistent task execution.
- Identify and mitigate potential hazards.
- Provide important safety information to maintain safety standards.
- Ensure compliance with local regulations and industry standards.
👉 Try this construction site work instruction template for free.
User manual template
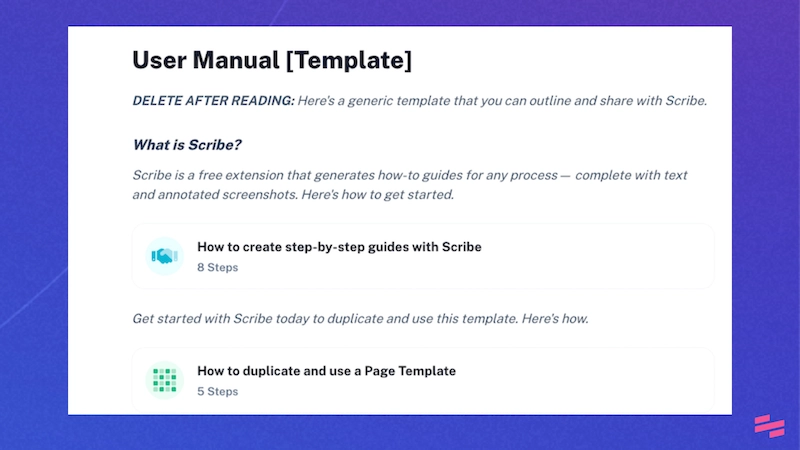
Customize this user manual template with step-by-step visual instructions on setup, operation, maintenance, and more.
👉 Try this user manual template for free.
Instruction manual template
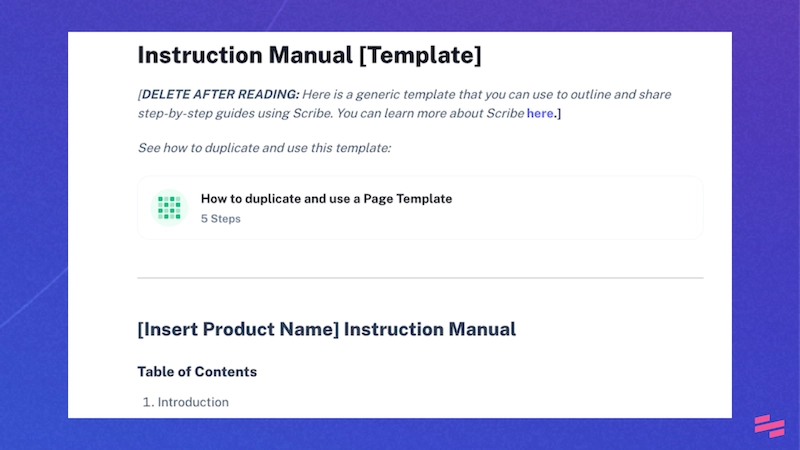
Use this instruction manual template to provide users with the information they need for:
- Cleaning and maintenance.
- Adjusting settings.
- Changing parts.
- Troubleshooting common issues.
👉 Try this instruction manual template for free.
Wrapping up: operation and maintenance manual
O&M manuals reduce the risk of accidents, prevent loopholes in quality control and eliminate inefficiencies. These manuals can also train and support employees in several scenarios.
At its core, a good operations and maintenance manual brings transparency to your organization and creates opportunities for growth.
Sign up for Scribe (it’s free!) and create your first operation and maintenance manual in minutes!