Introduction
The business environment is ever-evolving. Organizations that are still clinging to conventional practices may eventually perish. Focusing on continuous improvement is crucial to stay ahead of the competition. That means you should constantly assess your business processes. It will help identify the scope for improvement, limit bottlenecks, and implement proven practices.
Unfortunately, it is easier said than done. Nearly 50 percent of process improvement strategies fail. With the right tools, you can successfully practice continuous improvement cycles.
Here are our top picks for 9 tools for continuous improvement to get you started. Amplify your business performance and reduce costs through cutting-edge continuous improvement software.
TL;DR: Best continuous improvement software in 2025
- Impruver
- Process Street
- KaiNexus
- KPI Fire
- The Lean Way
- Q-Optimize
- Braineet
- Planbox
- Bonus continuous improvement software: Scribe
{{banner-short-v2="/banner-ads"}}
What is continuous improvement software?
Continuous improvement is the foundation upon which modern businesses are built. It is an ongoing, long-term approach to improving products, processes, and services through breakthrough and incremental improvements. It effectively identifies opportunities that help streamline operations, improve efficiency, and reduce wastage.
When the business environment changes rapidly, you must avoid following old practices and making the same mistakes. This is where continuous improvement can add value to your business. It is a way to implement a continuous process improvement model across all aspects of your organization.
However, implementing a culture of continuous improvement organization-wide can be challenging. Using robust and intuitive software can streamline implementing and sustaining the culture of constant improvement. It functions on three principles — communicated goals, employee involvement, and knowledge & skills sharing.
9 best continuous improvement software
1: Impruver
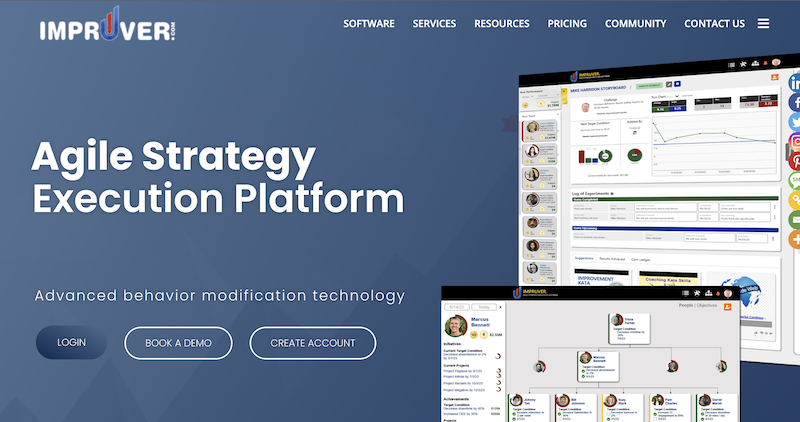
G2 Rating: Not available
Capterra Rating: Not available
Impruver Pricing: Free action board; $6.25 per month per user
Impruver Overview:
Impruver is an agile strategy execution software that aids in effective continuous improvement. The constant improvement software helps improve business efficiency, reduce waste, and ensure effective cost management. It is designed on three principles – The 4 Disciplines of Execution, scientific leadership, and Toyota KATA.
Use the software to develop an internal talent base and facilitate leadership coaching. It helps augment your people’s problem-solving capabilities and continuously improves results. The platform offers an entire suite of rich and user-friendly features. It allows organizations to focus on innovation and engage employees meaningfully. Take a data-driven approach to develop scientific thinking to address business challenges.
The software is cloud/SaaS-based, but you can also access it via a mobile app.
2: Process Street
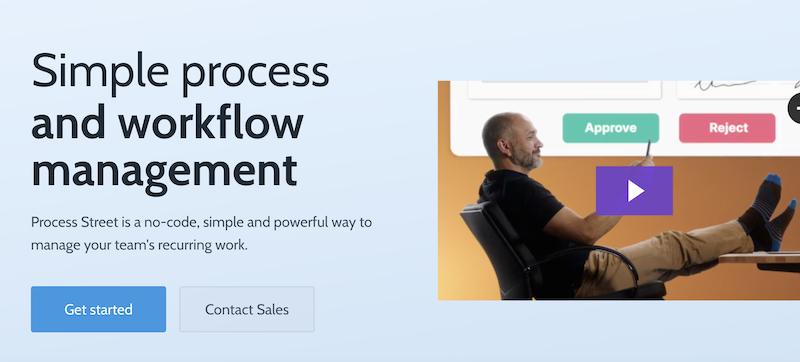
G2 Rating: 4.6
Capterra Rating: 4.7
Process Street Pricing: 14-day free trial period; paid plans start at $100/month or $1,000 billed annually
Process Street Overview:
Repetitive tasks can pull down the operational efficiency of a business. Process Street is a continuous improvement software that helps improve repeat work and drive consistent growth. Considering constant improvement can be complex, the software allows you to document, change, track, and analyze your processes.
Use the simple and intuitive drag-and-drop editor to create checklist templates for your recurring processes. A User-friendly interface and robust features enable you to get started with the software quickly. A centralized hub allows you to develop, store, launch, and access process templates.
With Process Street, you can easily edit and deploy all your improvements with a single click. Create sequential, multi-stage, or single-instance approvals to streamline the authorization process. During the free trial period, you can create unlimited workflows and pages.
See our Process Street alternatives for a list of the top software options.
3: KaiNexus
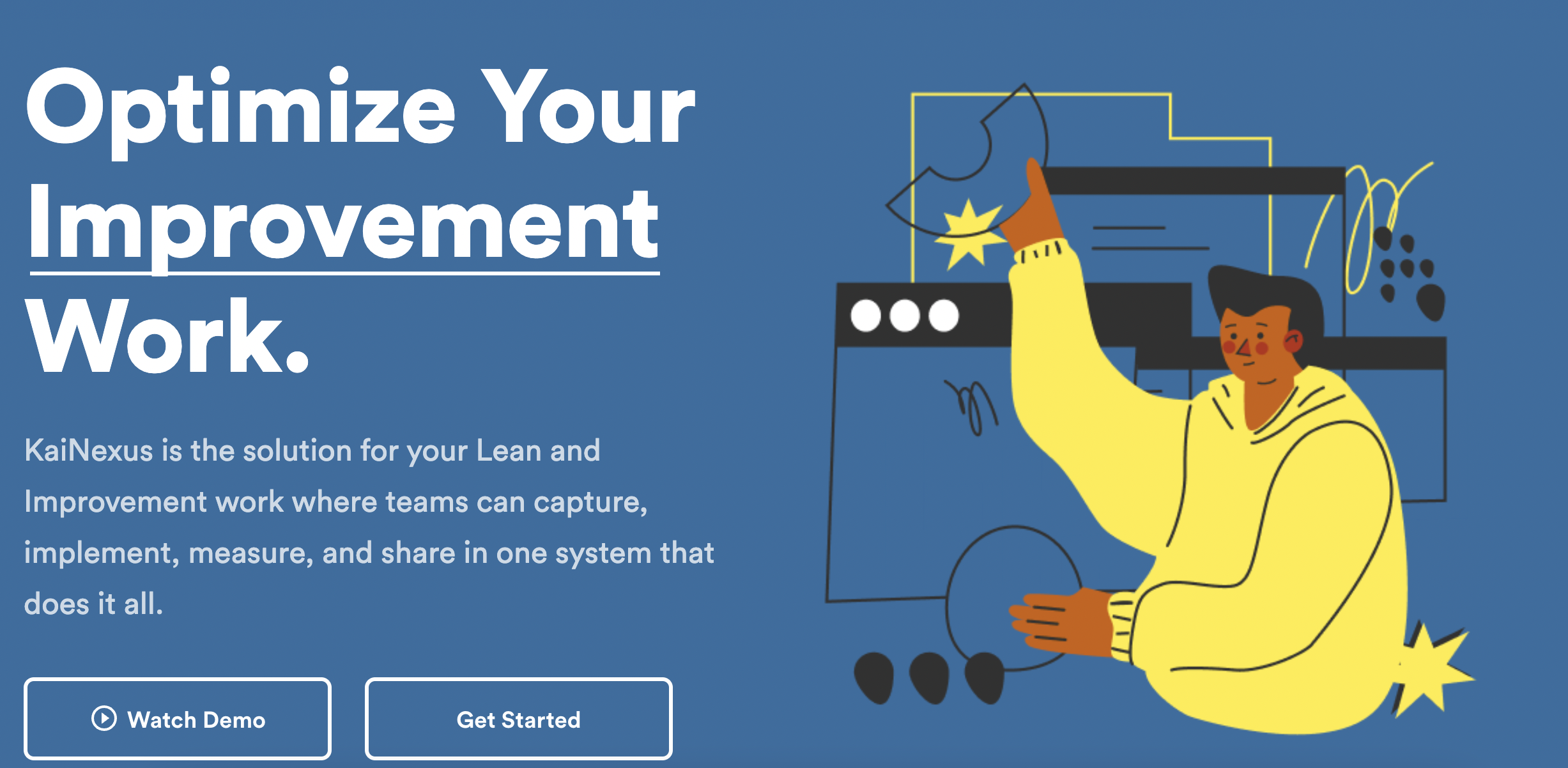
G2 Rating: 5
Capterra Rating: Not available
KaiNexus Pricing: Custom pricing
KaiNexus Overview:
Promoting a culture of continuous improvement is one of the biggest challenges any organization faces. It is where KaiNexus comes into the picture. The software supports implementing a culture of improvement enterprise-wide and through all stages. It is an ideal platform for starting, spreading, or sustaining continuous improvement.
It is a cutting-edge platform to engage your people for both top-down and bottom-up improvements. The software comes with a full suite of features. These include virtual visual management boards, workflows, knowledge sharing, team collaboration, detailed reports, and notifications.
KaiNexus is an all-in-one platform to streamline and standardize your process improvement.
4: KPI Fire
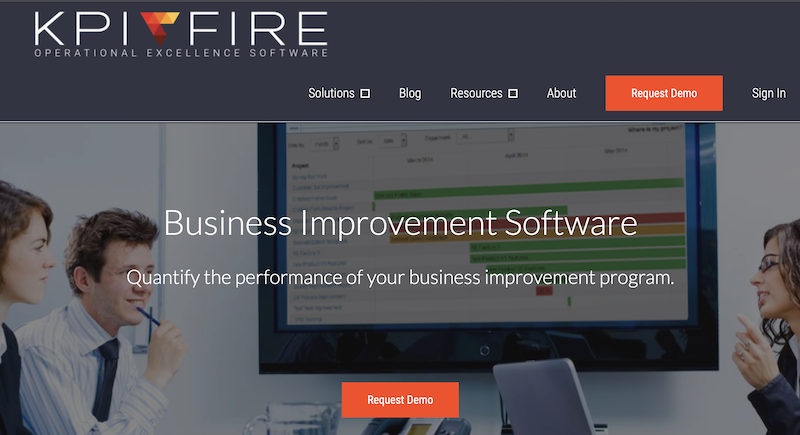
G2 Rating: 4.5
Capterra Rating: 4.7
KPI Fire Pricing: Custom pricing
KPI Fire Overview:
KPI Fire is a leading-edge continuous improvement and strategy execution software. It can help organizations switch from spreadsheets and take their projects and strategic goals into a collaborative environment. It helps promote a culture of improvement and allows teams to succeed.
The software will enable you to capture innovative ideas that can help drive improvement. Thoughts bring variation and help eliminate waste. The Idea Funnel will enable you to pick and organize the best ideas and transform them into projects.
The Effort vs. Impact Matrices allow you to evaluate and prioritize ideas.
Adopt a standardized problem-solving approach with a library of workflows, such as Kaizen, DMAIC, 8Ds, and more. These workflows have customizable templates and forms that can adapt to your training needs. Additionally, the software enables you to design your workflow.
5: The Lean Way
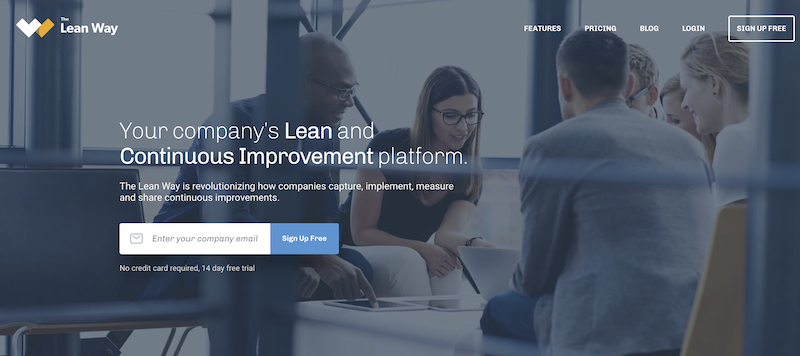
G2 Rating: 4.5
Capterra Rating: Not available
The Lean Way Pricing: 14-day free trial available; paid plans start at $20 per user per month
The Lean Way Overview:
The Lean Way is a robust continuous improvement software. It allows organizations to capture, implement, track, and share continuous improvement enterprise-wide. The platform promotes a culture of lean thinking, enabling teams to identify opportunities for improvement. You can also identify bottlenecks and measure the progress of every modification. The software also allows you to implement more improvements, achieving maximum impact.
Use the Lean Way to promote continuous improvement & Kaizen. It comes with a broad range of Lean tools that allow you to foster a culture of improvement. The Knowledge Wall lets you keep your teams updated on new enhancements and facilitates communication. It also allows teams to identify further improvements and minimize waste.
The free trial period gives you access to the Knowledge Wall, Boards, Improvements, Widgets, and full customization. Widgets allow you to track your company’s performance with data-driven charts and custom figures. You also get numerous other tools and features to implement continuous improvement.
6: Q-Optimize
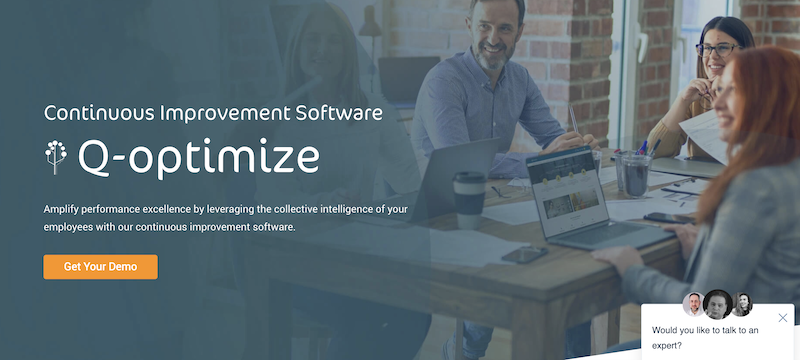
G2 Rating: 4.5
Capterra Rating: 4.8
Q-Optimize Pricing: Not listed
Q-Optimize Overview:
Q-Optimize, a segment of Qmarkets, is a leading-edge continuous improvement software that can help streamline your business operations. It allows you to use the collective intelligence of your people, which can facilitate the process of constant improvement.
The software is all-encompassing, including diverse phases of improvement. These include gathering ideas, evaluating, approving, implementing, and measuring ROI. With Q-Optimize, you get access to a broad range of tools. These include idea evaluation workflows, project tracking, role definition, permission control, and powerful reporting.
The software is fully optimized and responsive to view improvements on any device. Intuitive and straightforward self-admin functionality helps save time and costly training. Use custom branding and other tools to improve business processes and reduce waste.
7: Braineet
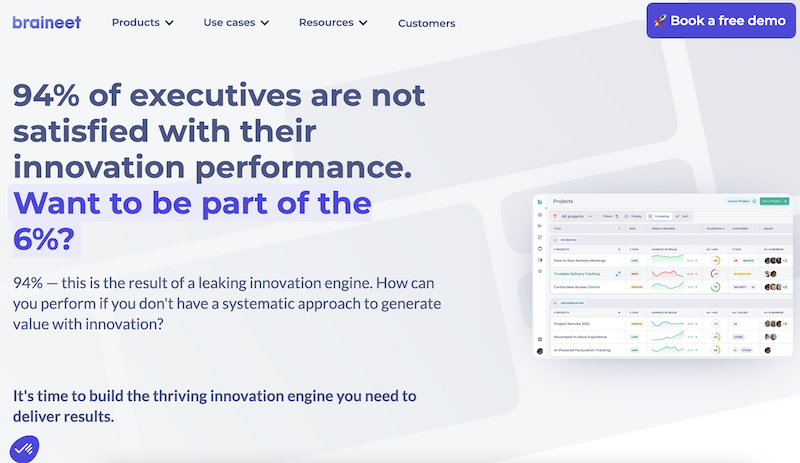
G2 Rating: 5
Capterra Rating: 5
Braineet Pricing: Get custom pricing
Braineet Overview:
In today’s fast-evolving environment, every organization needs to innovate and get more agile to facilitate continuous improvement. And what’s what Braineet empowers you to do – improve your innovation performance. The software was designed with the idea of fostering innovation. It is one of the foundations of successful continuous improvement.
Braineet allows you to create an innovation engine that guides the team and enables them to make better decisions. The software has many proven templates that provide a clear path for your teams to follow. They know what to do, what’s next, and what was done in the past.
The software provides a personalized portfolio dashboard. It allows you to define your KPIs and gather the correct datasets. You can seamlessly track anything through the dashboard. Gain visibility of your portfolio levels and projects, and make informed decisions. Centralize files and knowledge through Braineet Workflow.
8: Planbox

G2 Rating: 4.9
Capterra Rating: 4.8
Planbox Pricing: Get custom pricing
Planbox Overview:
Planbox is an agile innovation management suite. It is a modular platform that aids in many functions – Ecosystem Enablement, Emerging Tech Empowerment, and Innovation Portfolio Management. Their continuous improvement platform functions as a robust framework. It aids in problem discovery, cross-functional collaboration, solution development, and analysis.
Take a challenge-driven approach to integrate an innovation management system. Planbox paves the way for agile innovation. Elsewhere, you can also launch activities that help boost innovation visibility, engagement, and accessibility organization-wide. You can undertake different activities: Innovation Jam, Decision Making & Problem Solving, Challenge-Driven Innovation, etc.
9: Bonus Continuous Improvement Software: Scribe
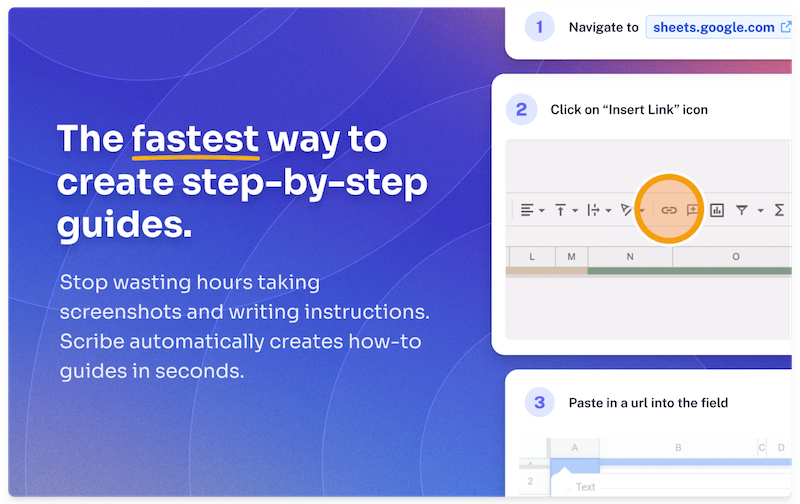
G2 Rating: 4.8
Capterra Rating: 4.9
Scribe Pricing: Free basic plan
Scribe Overview:
Scribe is not continuous improvement software in the standard sense. However, it helps create powerful process documents. You can create process documentation using Scribe to implement a change, train your employees, and foster a culture of continuous improvement.
Simply turn on the Scribe extension and go through your process as usual. Scribe auto-generates a step-by-step guide, complete with annotated screenshots and text, in seconds.
Here's how it works.
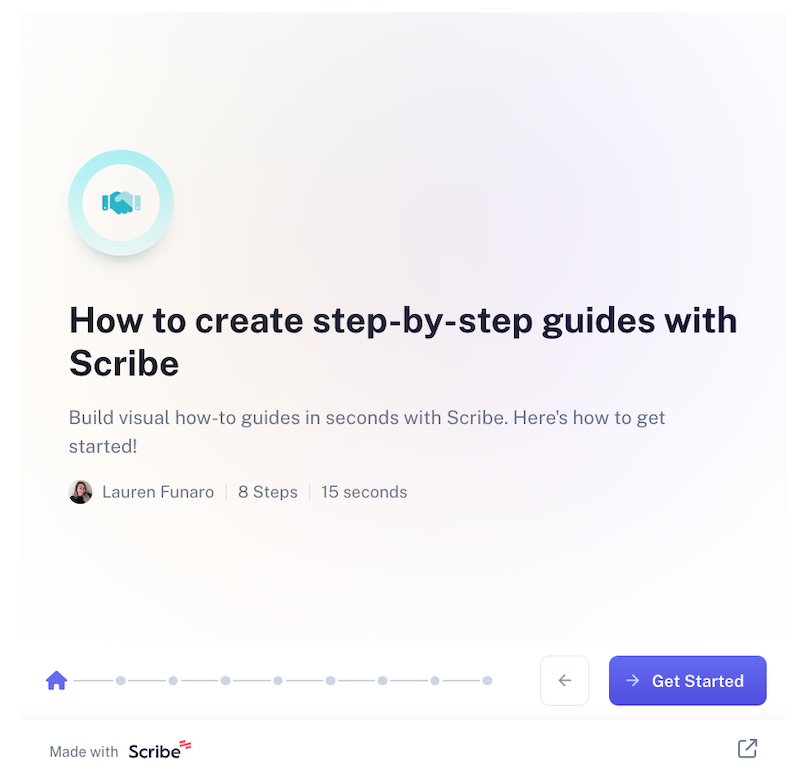
You can create custom process documents, how-to guides, SOPs, training, and much more. Use Scribe Pages to combine multiple guides, videos, images, GIFs and more. You can ask the AI to add titles and descriptions — or ask it to write the documents for you with a simple prompt.
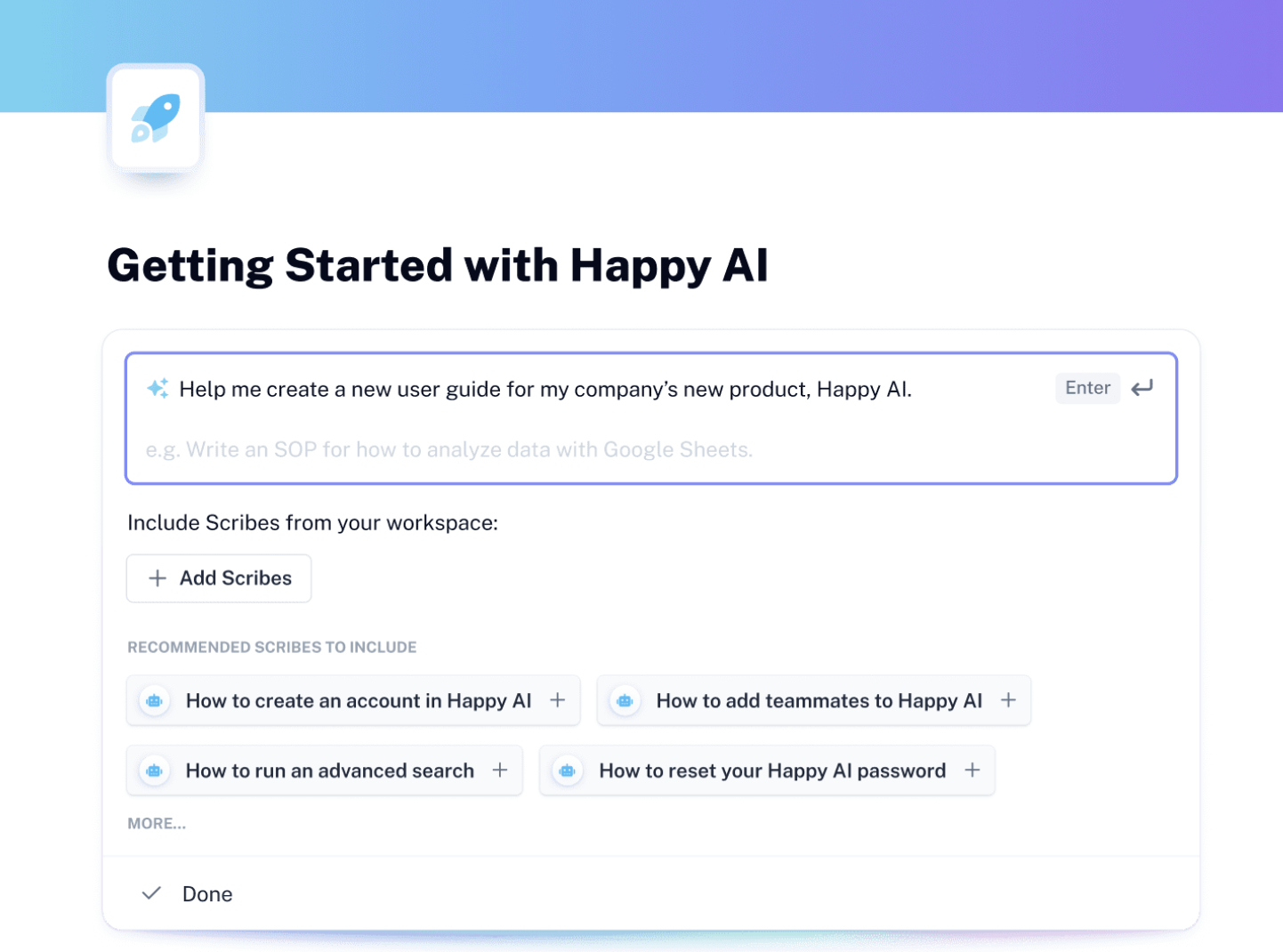
Share these with your teams anywhere with one click. Send a link, export to PDF or HTML formats, or embed in your wiki, knowledge base or other platform. Scribe integrates with thousands of popular apps like SharePoint, Confluence and Notion.
{{banner-default="/banner-ads"}}
Key features of continuous improvement software
Good continuous improvement software has the following essential features:
- Real-time visibility on key improvement opportunities
- Operations control and audit tools
- Meeting management platform integration
- Seamless search & documentation options
- Robust employee engagement tools
- Simple and intuitive user interface
Why you need continuous improvement software
Here’s why it is crucial to have continuous improvement software:
- Identify and prioritize improvement opportunities.
- Streamline operations to minimize the time your team spends in completing complex processes.
- Automate processes to reduce errors.
- Facilitates organization-wide communication and collaboration to promote a culture of continuous improvement.
- Improve operational efficiency and reduce waste.
Final thoughts: continuous improvement software
The current business landscape is competitive, so continuous improvement is essential. Investing in cutting-edge technologies can help improve efficiency and identify opportunities for improvements.
The best continuous improvement software has robust features that aid innovation, creativity, engagement, problem-solving, data tracking, and reporting. With numerous great platforms to choose from, here are some things to consider when making your decision:
- It should incorporate three crucial elements – Enterprise Resource Planning, Quality Management System, and Business Process Management.
- Does the software allow gathering data that is crucial to your operations? Or is data gathering limited to what the software offers?
- Is it a closed-loop system that provides valuable data on whether the goals are moving in the right direction?
- Does it help identify the gaps in operational goals and processes?
- Can I scale the software as the business needs change?
- Check the pricing model. You would want software that scales to your business needs without a large subscription or license cost. See if the software comes with a free trial period.
It is the right time to implement continuous improvement in your organization. And the right software is here to help you make the improvements. Typically, the software is cloud-based. It enables you to keep records of change and access the same quickly. By digitizing your business-critical data, you can track improvement opportunities and growth more efficiently.
Based on our analysis, here is a quick summary of the top continuous improvement software:
- Overall good: Q-Optimize and KaiNexus
- Innovation management: Planbox
- Strategy management: KPI Fire
- Process documentation: Scribe
Jumpstart today to continuous improvement with cutting-edge software. These are designed to help you identify more opportunities, build a culture, promote collaboration, and improve operational efficiency. Free trials allow you to test the software before investing time and money.
Whatever software you choose, make sure your team has the knowledge and training to adapt to the same. Only then can it help achieve improved operational efficiency.
There are many different continuous improvement software options, so it can take time to decide which is right for your business.